Компьютерные технологии в производстве полимерной тары и упаковки
1 февраля 2007
// engineering.ru |
Сегодня, видимо, уже ни у кого не возникает сомнений в том, что дальнейшее совершенствование технологий производства полимерной тары и упаковки, начиная от разработки дизайна и конструкции будущего изделия и кончая выходом готовой продукции, невозможно без использования современной компьютерной техники. В первую очередь, это определяется теми экономическими выгодами, которые приносит использование компьютерных технологий вообще. Вместе с тем, совершенно очевидно, что реализация компьютерных технологий возможна лишь при наличии специального программного обеспечения: прикладных компьютерных программ, позволяющих решать конкретные технические задачи.
В настоящее время рынок программного обеспечения предлагает достаточное число продуктов для компьютерного конструирования технических объектов вообще (CAD-системные продукты). Однако, сам процесс конструирования предполагает наличие необходимой базы исходных данных, являющихся результатом решения достаточно сложных инженерных задач как конструкторского, так и технологического уровней. Решение таких сложных задач может быть реализовано только на базе современной компьютерной техники и при наличии специального программного обеспечения. В отличие от рынка CAD-системных продуктов, рынок программного обеспечения для компьютерного инжиниринга (CAE) технологических процессов переработки полимерных материалов в изделия и детали, в том числе в тару и упаковку, в силу ряда причин, находится, пока ещё, только в стадии своего формирования, но уже сейчас предлагает разработчикам оборудования для литьевого и раздувного формования полимерной тары, а также предприятиям, производящим ее, ряд различных программных продуктов, разработанных российскими специалистами. Так, например, программные продукты «Пластик — 2D,3D» позволяют реализовать автоматизированное проектирование литьевой тары из термопластичных полимеров на базе двух- и трёхмерного моделирования процесса формования.
Рис.1. Схема процесса экструзионно-раздувного формования:
1 — кольцевая экструзионная головка; 2 — экструзионная заготовка;
3- раздувной ниппель; 4 – раздувные полуформы; 5 – полое изделие
Его использование позволяет еще на стадии разработки конструкции изделия оценить его «технологичность», соответствие параметров изделия техническим или эксплуатационным требованиям, например, по разнотолщинности, максимальной или минимальной толщине стенки и т.д.; определять необходимые параметры экструзионной заготовки, используемой для формования изделия; оценивать необходимость «программирования» толщины стенки используемой заготовки и т.
Другой программный продукт – «Extrusion heads» – также ориентирован на экструзионно-раздувные технологии производства полимерной тары и упаковки, в том числе и на технологии производства рукавных плёнок, и позволяет в автоматизированном режиме рассчитывать геометрические параметры дорнов и мундштуков кольцевых экструзионных головок, обеспечивающих экструзию рукавных заготовок необходимых геометрических размеров.
Особое внимание конструкторов и технологов, связанных не только с производством полимерной тары, но и с любыми другими технологическими процессами переработки пластмасс, хотелось бы обратить на уникальный программный продукт «REOCON». Суть в том, что ни один технологический процесс переработки полимеров не может быть оптимально реализован без знания фундаментальных реологических характеристик перерабатываемого полимерного сырья, равно, как и ни один вид перерабатывающего оборудования не может быть рационально сконструирован без их учета.
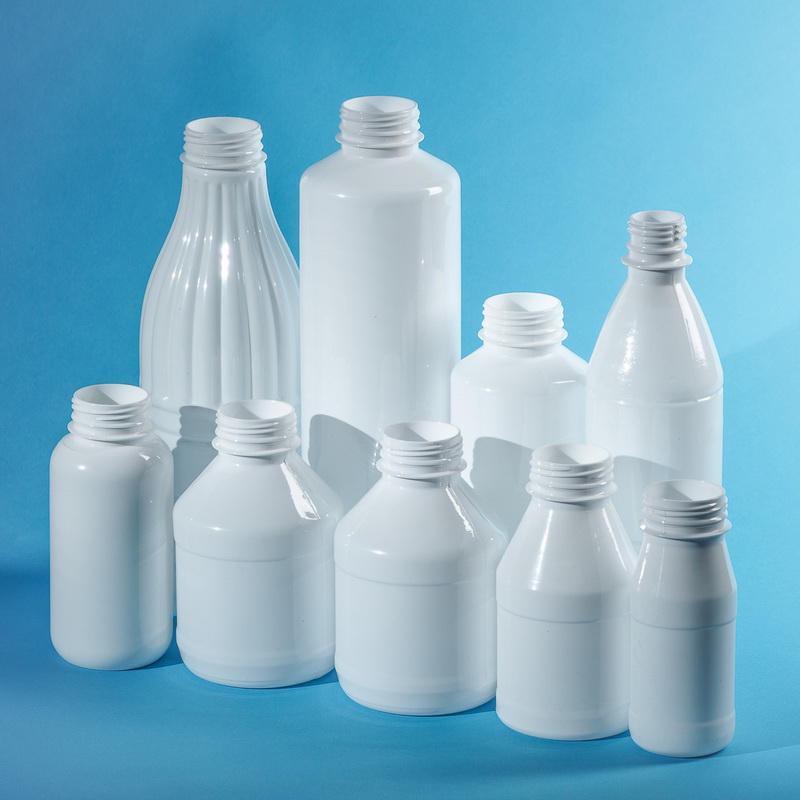
В заключение следует отметить, что практика использования вышеперечисленных CAE-системных программных продуктов применительно к технологиям экструзионно-раздувного и литьевого формования полимерной тары и упаковки, конструированию соответствующих видов оборудования и формующего инструмента подтверждает их высокую эффективность и соответствие уровню современного производства.
Список литературы
1. Б. В. Бердышев, В. К. Скуратов, Ю. Г. Иванов. Компьютерное моделирование процесса раздувного формования полых изделий из экструзионных заготовок.. «Пластические массы», 1994, №1. с.26-30.
Производство пластиковой тары методом экструзии
Упаковка из пластика сейчас активно используется во всех сферах производства, ведь именно этот вид тары отвечает одновременно максимальному количеству требований: по надежности и прочности, возможности производить изделия любой формы, низкому весу и демократичной цене. АО «Термопласт» изготавливает пластмассовую и пластиковую тару на заказ с доставкой по Санкт-Петербургу. Наши современные производственные линии обеспечивают максимальную эффективность экструзионно-выдувного формования. Гарантия качества и оптимизация расходов: вы получаете первоклассные изделия по выгодным расценкам.
Банки и бутылки из ПНД и ПВД, полистирола и полипропилена – это идеальная тара для химии и косметической продукции. Наша пластиковая упаковка востребована для фасовки всевозможных жидких, гелеобразных, сыпучих и твердых товаров. Получение полых изделий из термопластов способом экструзии было одним из первых технологических решений в этой сфере. Теперь, с более продвинутым оснащением, эта технология получила новое дыхание.
Экструзионно-выдувное формование
Для создания баночек, канистр, бутылок и других емкостей из ПВД и ПНД необходим следующий набор оборудования:
— экструзионно-выдувная машина;
— компрессор с ресиверами, подающий сжатый воздух под нужным давлением;
— охлаждающий пресс-формы и масло в гидроприводе чиллер;
— установка, дробящая отхода для повторного использования.
Процесс создания полимерной тары выглядит так: рабочая смесь (гранулированный термопласт + необходимые красители) подается в экструдер. По нему она перемещается с помощью шнека или (реже) поршня. Под тепловым и механическим воздействием на выходе получается расплавленная однородная масса нужной температуры. Сквозь трубную головку смесь выдавливается вниз – в виде уже цилиндрической заготовки она попадает в открытую заранее изготовленную пресс-форму из двух симметричных половин. Когда заготовка достигнет нужной длины, форма смыкается и отделяется от головки при помощи особого ножа.
С одной стороны при этом (обычно снизу) заготовка сваривается, а с противоположной формируется отверстие – особое приспособление подает сквозь него сжатый воздух внутрь заготовки. Под давлением воздуха горячий и эластичный материал раздувается, принимая очертания внутренних стенок формы.
Во внутренних полостях пресс-форм постоянно циркулирует вода, потому их холодные стенки быстро охлаждают и полимер отвердевает. После этого следует лишь разъединить половины формы, извлечь готовое изделие и удалить при надобности излишки материала.
Преимущества такого способа производства пластиковых банок и бутылок таковы:
1) Возможность задавать толщину стенок емкостей с максимальной точностью.
2) Уникальная среди других способов производства пластиковых изделий возможность создавать канистры, бутыли и другую тару сразу с ручкой. Нет необходимости отливать ручку отдельно и потом крепить к изделию.
3) При работе с расплавленным материалом возможно самое точное выполнение сложных поверхностей – формирование рисунков, бордюров, надписей, логотипов и так далее.
4) Огромное разнообразие продукции, которую можно изготавливать этим методом. Мы разрабатываем пресс-формы на заказ для производства оригинальных, эксклюзивных пластиковых изделий.
5) При использовании сразу нескольких экструдеров с различными видами пластиков можно изготавливать многослойную тару – она увеличивает срок хранения расфасованной в нее продукции в несколько раз.
Руководство по производственным процессам для пластмасс
Пластмассы являются наиболее распространенными материалами для производства деталей и изделий конечного использования, от потребительских товаров до медицинских устройств. Пластмассы — это универсальная категория материалов с тысячами вариантов полимеров, каждый из которых имеет свои особые механические свойства. Но как изготавливаются пластиковые детали?
Было разработано множество процессов производства пластмасс, охватывающих широкий спектр применений, геометрий деталей и типов пластмасс. Для любого проектировщика и инженера, занимающегося разработкой продукции, очень важно быть знакомым с вариантами производства, доступными сегодня, и новыми разработками, которые показывают, как детали будут производиться завтра.
В этом руководстве представлен обзор наиболее распространенных производственных процессов для изготовления пластиковых деталей, а также рекомендации, которые помогут вам выбрать наилучший вариант для вашей области применения.
При выборе производственного процесса для вашего продукта учитывайте следующие факторы:
Форма: У ваших деталей есть сложные внутренние особенности или жесткие требования к допускам? В зависимости от геометрии конструкции варианты изготовления могут быть ограничены или может потребоваться значительная оптимизация конструкции для производства (DFM), чтобы сделать их производство экономичным.
Объем/стоимость: Какой общий или годовой объем деталей вы планируете производить? Некоторые производственные процессы имеют высокие первоначальные затраты на инструменты и настройку, но производят детали, которые недороги в расчете на одну деталь. Напротив, производственные процессы с малым объемом производства имеют низкие начальные затраты, но из-за более медленного времени цикла, меньшего количества автоматизации и ручного труда стоимость одной детали остается постоянной или снижается лишь незначительно при увеличении объема.
Время выполнения: Как быстро вам нужно изготовить детали или готовую продукцию? Некоторые процессы создают первые детали в течение 24 часов, в то время как подготовка инструментов и настройка для некоторых крупносерийных производственных процессов занимают месяцы.
Материал: Каким нагрузкам и напряжениям должен противостоять ваш продукт? Оптимальный материал для данного применения определяется рядом факторов. Стоимость должна быть сбалансирована с функциональными и эстетическими требованиями. Рассмотрите идеальные характеристики для вашего конкретного применения и сравните их с доступными вариантами в данном производственном процессе.
Загрузите версию этой инфографики в высоком разрешении здесь.
Видеоруководство
Не можете найти лучшую технологию 3D-печати для ваших нужд? В этом видеоруководстве мы сравниваем технологии FDM, SLA и SLS с учетом популярных соображений покупателей.
Смотреть видео
Пластмассы бывают тысяч разновидностей с различными базовыми химическими составами, производными и добавками, состав которых обеспечивает широкий спектр функциональных и эстетических свойств.
Чтобы упростить процесс поиска материала, наиболее подходящего для данной детали или продукта, давайте сначала рассмотрим два основных типа пластика: термопласты и реактопласты.
Термопласты являются наиболее часто используемым типом пластика. Главной особенностью, которая отличает их от реактопластов, является их способность проходить через многочисленные циклы плавления и затвердевания без существенной деградации. Термопласты обычно поставляются в виде небольших гранул или листов, которые нагреваются и формируются в желаемую форму с использованием различных производственных процессов. Процесс полностью обратим, так как не происходит химического связывания, что делает возможной переработку или плавление и повторное использование термопластов.
Распространенные типы термопластичных материалов:
- Акрил (ПММА)
- Акрилонитрилбутадиенстирол (АБС)
- Полиамид (ПА)
- Полимолочная кислота (PLA)
- Поликарбонат (ПК)
- Полиэфирэфиркетон (PEEK)
- Полиэтилен (ПЭ)
- Полипропилен (ПП)
- Поливинилхлорид (ПВХ)
В отличие от термопластов, термореактивные пластмассы (также называемые термореактивными) после отверждения остаются в постоянном твердом состоянии. Полимеры в термореактивных материалах сшиваются в процессе отверждения под действием тепла, света или подходящего излучения. Этот процесс отверждения образует необратимую химическую связь. Термореактивные пластмассы разлагаются при нагревании, а не плавятся, и не восстанавливаются при охлаждении. Переработка термореактивных материалов или возврат материала обратно в его основные ингредиенты невозможна.
Распространенные типы термопластичных материалов:
- Сложный эфир цианата
- Эпоксидная смола
- Полиэстер
- Полиуретан
- Силикон
- Вулканизированная резина
- 3D-печать
- Обработка с ЧПУ
- Полимерное литье
- Ротационное формование
- Вакуумное формование
- Литье под давлением
- Экструзия
- Выдувное формование
3D-принтеры создают трехмерные детали непосредственно из моделей САПР, создавая материал слой за слоем, пока не будет сформирована полная физическая деталь.
- Настройка печати: Программное обеспечение для подготовки к печати используется для ориентации и компоновки моделей в объеме сборки принтера, добавления поддерживающих структур (при необходимости) и разделения поддерживаемой модели на слои.
- Печать: Процесс печати зависит от типа технологии 3D-печати: моделирование методом наплавления (FDM) расплавляет пластиковую нить, стереолитография (SLA) отверждает жидкую смолу, а селективное лазерное спекание (SLS) сплавляет порошкообразный пластик.
- Постобработка: По завершении печати детали удаляются из принтера, очищаются или промываются, подвергаются постотверждению (в зависимости от технологии) и удаляются опорные конструкции (если применимо).
Поскольку 3D-принтеры не требуют инструментов и требуют минимального времени настройки для нового дизайна, стоимость изготовления нестандартной детали незначительна по сравнению с традиционными производственными процессами.
Процессы 3D-печати, как правило, медленнее и трудоемче, чем производственные процессы, используемые для массового производства.
По мере совершенствования технологий 3D-печати стоимость одной детали продолжает снижаться, открывая более широкий спектр приложений для малых и средних объемов.
3D Printing | |
---|---|
Form | High degree of freedom |
Lead time | Less than 24 hours |
Cycle time | |
Setup cost | $ |
Cost per part | $$$ |
Volume | Low to mid-volume applications (~1-1000 parts) |
В то время как для большинства процессов производства пластмасс требуется дорогостоящее промышленное оборудование, специальные помещения и квалифицированные операторы, 3D-печать позволяет компаниям легко создавать пластмассовые детали и быстрые прототипы на месте.
Компактные настольные или настольные системы 3D-печати для создания пластиковых деталей доступны по цене и требуют очень мало места и не требуют специальных навыков, что позволяет профессиональным инженерам, дизайнерам и производителям ускорить итерации и производственные циклы с дней или недель до нескольких часов.
На рынке представлено множество типов 3D-принтеров и технологий 3D-печати, а доступные материалы зависят от технологии.
Материалы для 3D-печати | |
---|---|
Fused deposition modeling (FDM) | Various thermoplastics, mainly ABS and PLA |
Stereolithography (SLA) | Thermoset resins |
Selective laser sintering (SLS) | Thermoplastics, typically nylon and его композиты |
Белая книга
Ищете 3D-принтер для печати ваших 3D-моделей в высоком разрешении? Загрузите наш технический документ, чтобы узнать, как работает SLA-печать и почему это самый популярный процесс 3D-печати для создания моделей с невероятной детализацией.
Загрузите информационный документ
Образец детали
Убедитесь сами и убедитесь в качестве Formlabs. Мы отправим бесплатный образец детали в ваш офис.
Запросить бесплатный образец Деталь
Обработка с ЧПУ включает в себя фрезерные станки, токарные станки и другие субтрактивные процессы, управляемые компьютером. Эти процессы начинаются с твердых блоков, стержней или стержней из металла или пластика, которым придают форму путем удаления материала путем резки, сверления, сверления и шлифования.
В отличие от большинства других процессов производства пластмасс, обработка с ЧПУ представляет собой вычитающий процесс, при котором материал удаляется либо вращающимся инструментом и неподвижной частью (фрезерование), либо вращающейся частью с неподвижным инструментом (токарный станок).
- Настройка задания: Для станков с ЧПУ требуется промежуточный этап создания и проверки траекторий движения (CAD в CAM).
Траектории инструмента управляют тем, где перемещаются режущие инструменты, с какой скоростью и какой сменой инструмента.
- Обработка: Траектории инструмента отправляются на станок, где начинается данный процесс вычитания. В зависимости от желаемой формы конечного продукта может потребоваться установить заготовку в новое положение, чтобы головка инструмента могла достигать новых областей.
- Постобработка: После изготовления деталь очищается и зачищается, обрезается.
Механическая обработка идеально подходит для небольших объемов пластиковых деталей, требующих жестких допусков и геометрии, которую трудно формовать. Типичные области применения включают прототипирование и детали конечного использования, такие как шкивы, шестерни и втулки.
CNC-обработка имеет низкую или умеренную стоимость настройки и позволяет производить высококачественные пластиковые компоненты в кратчайшие сроки из широкого спектра материалов.
Процессы обработки имеют больше ограничений по геометрии детали, чем 3D-печать. При механической обработке стоимость детали увеличивается с увеличением сложности детали. Подрезы, проходы и элементы на нескольких поверхностях деталей увеличивают стоимость детали.
Процессы обработки требуют припусков на доступ к инструменту, а определенные геометрические формы, такие как изогнутые внутренние каналы, трудно или невозможно изготовить с помощью обычных методов вычитания.
Обработка с ЧПУ | |
---|---|
Form | Medium degree of freedom |
Lead time | Less than 24 hours |
Cycle time | |
Setup cost | $$ |
Cost per part | $$$$ |
Объем | Обработка малых и больших объемов (~1-5000 деталей) |
Большинство твердых пластиков можно обрабатывать с некоторой разницей в сложности. Для более мягких термореактивных пластиков требуются специальные инструменты для поддержки деталей во время обработки, а пластики с наполнителями могут быть абразивными и сокращать срок службы режущего инструмента.
Некоторые часто обрабатываемые пластики:
- Акрил (ПММА)
- Акрилонитрилбутадиенстирол (АБС)
- Полиамид нейлон (ПА)
- Полимолочная кислота (PLA)
- Поликарбонат (ПК)
- Полиэфирэфиркетон (PEEK)
- Полиэтилен (ПЭ)
- Полипропилен (ПП)
- Поливинилхлорид (ПВХ)
- Поликарбонат (ПК)
- Полистирол (ПС)
- Полиоксиметилен (ПОМ)
Веб-семинар
На этом веб-семинаре вы узнаете, как проектировать и печатать на 3D-принтере приспособления и приспособления для замены механически обработанных деталей, а также узнаете о пяти способах повышения эффективности вашего производственного цеха с помощью 3D-печати.
Посмотреть вебинар сейчас
При литье полимеров реактивная жидкая смола или каучук заполняет форму, которая вступает в химическую реакцию и затвердевает. Типичные полимеры для литья включают полиуретан, эпоксидную смолу, силикон и акрил.
- Подготовка пресс-формы: Форма покрыта разделительной смазкой для облегчения извлечения из формы и часто предварительно нагревается до определенной температуры материала.
- Литье: Синтетическая смола смешивается с отвердителем и заливается или впрыскивается в форму, где она заполняет полость формы.
- Отверждение: Отливка отверждается в форме до тех пор, пока не затвердеет (для некоторых полимеров нагревание формы может ускорить время отверждения).
- Извлечение из формы: Форма открывается, и отвержденная деталь удаляется.
- Обрезка: Дефекты литья, такие как заусенцы, литники и швы, обрезаются или шлифуются.
Гибкие формы, изготовленные из латексной резины или силиконовой резины, вулканизированной при комнатной температуре (RTV), недороги по сравнению с твердой оснасткой, но могут производить лишь ограниченное количество (от 25 до 100) отливок в результате химической реакции уретанов, эпоксидных смол, полиэстера. , а акрил разрушает поверхности формы.
Полимерное литье является относительно недорогим, с небольшими первоначальными инвестициями, но термореактивные полимеры для литья обычно дороже, чем их термопластичные аналоги, а формование литых деталей является трудоемким. Каждая литая деталь требует некоторого ручного труда для последующей обработки, что делает конечную стоимость детали высокой по сравнению с автоматизированными методами производства, такими как литье под давлением.
Полимерное литье обычно используется для прототипирования, мелкосерийного производства, а также в некоторых стоматологических и ювелирных целях.
Polymer Casting | |
---|---|
Form | High degree of freedom |
Lead time | Less than 24 hours to a few days |
Cycle time | Minutes to multiple days , в зависимости от времени отверждения |
Стоимость установки | $ |
Cost per part | $$ |
Volume | Low volume applications (~1-1000 parts) |
- Polyurethane
- Эпоксидная смола
- Полиэфир
- Полиэстер
- Акрил
- Силикон
Ротационное формование (также называемое ротационным формованием) представляет собой процесс, включающий нагревание полой формы, заполненной порошкообразным термопластом, и вращение вокруг двух осей для производства в основном крупных полых изделий. Процессы центробежного формования термореактивных пластмасс также доступны, однако менее распространены.
- Зарядка: Порошок пластика загружается в полость формы, а затем устанавливаются остальные части формы, закрывая полость для нагрева.
- Нагрев: Форму нагревают до тех пор, пока пластиковый порошок не расплавится и не прилипнет к стенкам формы, при этом форму вращают вдоль двух перпендикулярных осей для обеспечения однородного пластикового покрытия.
- Охлаждение: Форма медленно охлаждается, в то время как форма остается в движении, чтобы гарантировать, что оболочка детали не провиснет и не разрушится до полного затвердевания.
- Удаление детали: Деталь отделяется от формы, любые заусенцы обрезаются.
Для ротационного формования требуются менее дорогие инструменты, чем для других методов формования, поскольку в процессе для заполнения формы используется центробежная сила, а не давление. Формы могут быть изготовлены, обработаны на станке с ЧПУ, отлиты или сформированы из эпоксидной смолы или алюминия с меньшими затратами и намного быстрее, чем инструменты для других процессов литья, особенно для крупных деталей.
Ротационное формование позволяет создавать детали с практически одинаковой толщиной стенок. После того, как инструменты и процесс настроены, стоимость одной детали становится очень низкой по сравнению с размером детали. Также можно добавить в форму готовые детали, такие как металлическая резьба, внутренние трубы и конструкции.
Эти факторы делают ротационное формование идеальным для мелкосерийного производства или в качестве альтернативы выдувному формованию для небольших объемов. Типичные продукты ротационного формования включают резервуары, буи, большие контейнеры, игрушки, шлемы и корпуса каноэ.
Ротационное формование имеет некоторые конструктивные ограничения, а готовые изделия имеют более низкие допуски. Поскольку вся пресс-форма должна нагреваться и охлаждаться, процесс также имеет длительное время цикла и является довольно трудоемким, что ограничивает его эффективность при больших объемах производства.
Rotational Molding | |
---|---|
Form | Medium degree of freedom, ideal for large hollow parts |
Lead time | Days to a few weeks |
Cycle time | Typically |
Стоимость установки | $$$ |
Стоимость за деталь | $$ |
Объем | Средний объем-5 (09~000 деталей)0154 |
Наиболее распространенным материалом для ротационного формования является полиэтилен (ПЭ), который используется в 80% случаев, главным образом потому, что ПЭ легко измельчается в порошок при комнатной температуре.
Обычно ротационно формованные пластмассы включают:
- Полиэтилен
- Полипропилен
- Поливинилхлорид
- Нейлон
- Поликарбонат
Вакуумное формование или термоформование – это производственный метод, при котором пластик нагревается и формуется, как правило, с использованием пресс-формы. Вакуум-формовочные машины различаются по размеру и сложности от недорогих настольных устройств до автоматизированного промышленного оборудования. Шаги ниже описывают типичный процесс промышленного вакуумного формования.
- Зажим: Пластиковый лист зажимается в раме.
- Нагрев: Лист и рама сдвинуты вплотную к нагревательным элементам, что делает пластик мягким и податливым.
- Вакуум: Рама опускается, пластик натягивается на форму, при этом включается вакуум, чтобы высосать весь воздух из пространства между пластиком и формой, формируя таким образом деталь.
- Охлаждение и разъединение: После того, как деталь была сформирована на форме, ей нужно дать время остыть перед удалением. Система охлаждения, такая как вентиляторы и распыляемый туман, иногда используются для сокращения времени цикла.
- Обрезка: После того, как деталь освобождена, лишний материал отрезается либо вручную, либо на станке с ЧПУ.
Затраты на инструменты для вакуумной формовки ниже по сравнению с другими методами формовки из-за малых усилий и давления. Формы изготавливаются из дерева, гипса или смолы, напечатанной на 3D-принтере, для мелкосерийного производства и нестандартных деталей. Для больших объемов производства производители используют более прочную металлическую оснастку.
Учитывая широкий спектр оборудования для термоформования и вакуумной формовки, а также возможности для автоматизации на самом высоком уровне, термоформование идеально подходит для любого применения, от изготовления нестандартных изделий или прототипов до массового производства. Однако этот процесс предлагает лишь ограниченную свободу форм и может использоваться только для изготовления деталей с относительно тонкими стенками и простой геометрией.
Части, формируемые под вакуумом, обычно включают упаковку продуктов, душевые поддоны, обивку дверей автомобилей, корпуса лодок и нестандартные изделия, такие как выравниватели зубов.
Vacuum Forming | |||||||||||||||||||||||||||||||||||||||||||||
---|---|---|---|---|---|---|---|---|---|---|---|---|---|---|---|---|---|---|---|---|---|---|---|---|---|---|---|---|---|---|---|---|---|---|---|---|---|---|---|---|---|---|---|---|---|
Form | Limited freedom, only thin-walled parts, no complex geometries | ||||||||||||||||||||||||||||||||||||||||||||
Lead time | Less than 24 hours to weeks | ||||||||||||||||||||||||||||||||||||||||||||
Cycle time | От секунд до минут, в зависимости от механизма | ||||||||||||||||||||||||||||||||||||||||||||
Стоимость настройки | $-$$$$ | ||||||||||||||||||||||||||||||||||||||||||||
Стоимость | $-$$$ | ||||||||||||||||||||||||||||||||||||||||||||
VOLUD | |||||||||||||||||||||||||||||||||||||||||||||
VOLUD | |||||||||||||||||||||||||||||||||||||||||||||
VOLUD | |||||||||||||||||||||||||||||||||||||||||||||
VOLUD | |||||||||||||||||||||||||||||||||||||||||||||
. термоформование, обеспечивающее гибкость в выборе материала. Пластмассы, обычно используемые для термоформования, включают:
Информационный документ Загрузите наш технический документ, чтобы узнать, как быстро создавать сложные формы с помощью 3D-печати, и узнать о советах и рекомендациях, которым следует следовать при подготовке деталей формы. Загрузить информационный документ Литье под давлением (IM) работает путем впрыскивания расплавленного термопластика в форму. Это наиболее широко используемый процесс для массового производства пластиковых деталей.
Пресс-формы для литья под давлением очень сложны и должны быть изготовлены с жесткими допусками для производства высококачественных деталей. Из-за высокой температуры и давления эти формы изготавливаются из металлов, таких как закаленная сталь. Более мягкие алюминиевые формы дешевле, но и изнашиваются быстрее, поэтому обычно используются для более умеренных производственных циклов. Литье под давлением можно использовать для изготовления очень сложных деталей, но некоторые геометрические формы значительно увеличат стоимость. Следование рекомендациям по проектированию для производства (DFM) поможет снизить затраты на инструменты. Создание новых пресс-форм для литья под давлением может занять месяцы, а их стоимость может исчисляться пяти- или шестизначными цифрами. Несмотря на высокие первоначальные затраты и медленное наращивание производства, литье под давлением не подходит для крупносерийного производства. После того, как инструмент настроен и запущен, время цикла занимает всего несколько секунд, и миллионы высококачественных деталей могут быть изготовлены за долю стоимости всех других производственных процессов.
|