Производство бетонных блоков: технология, оборудование, материалы
Производство бетонных блоков как массового строительного материала даже при современных объемах выпуска не в состоянии покрыть все потребности рынка. Стеновой блок, пустотелый, блок для внутренних перегородок и облегченный вид материала выпускается не только на промышленном оборудовании, но и даже на самодельных станках. Привлекательность этого вида бизнеса настолько велика, что многие выбирают именно его для начала деятельности, ведь для первого шага достаточно ровной площадки и формы для заливки бетона.
Технология производства
Для отливки стандартных бетонных блоков из песчано-бетонной смеси чаще всего применяется самая примитивная технология, не требующая при этом значительных капиталовложений и сложного оборудования. Технология производства бетонных блоков основывается на принципе равномерного застывания бетонной смеси в естественных условиях при нормальной температуре воздуха.
Моделью, иллюстрирующей процесс приготовления и застывания бетонного раствора, будет описание процесса заливки формы фундамента или монолитной плиты:
- Подготовка формы;
- Приготовление бетонного раствора;
- Заливка раствора в форму;
- Уплотнение раствора;
- Усадка смеси;
- Снятие опалубки;
- Окончательное высыхание смеси и набор рабочей твердости бетона.
В принципе такая схема вполне подходит для заливки большого объема бетона, но для бетонного блока для возведения стен она подходит лишь частично. Дело в том, что для формирования правильного прямоугольника с четкими гранями сторон, и гладкой поверхностью наружных граней необходимо применение бетонного раствора с минимальным содержанием воды. Таким образом, получается рассыпчатый бетон, который при попадании в форму и последующем уплотнением при помощи вибрации и давления пресса сбивается в плотную массу, способную держать форму.
Использование бетона с большим содержанием воды наоборот влечет за собой не формирование жесткой формы, а выдавливание из массы влаги, которая не способна выдерживать приданную ей жесткость, она попросту плывет.
При приготовлении раствора соблюдается очередность добавления компонентов — наполнитель, цемент, вода, пластификатор.
Технология изготовления предусматривает оптимизацию процесса производства за свет использования оборудования для производства бетонных блоков в виде вибростанка или виброплиты. В первом случае сформованный элемент остается сохнуть на площадке после снятия формы вибростанка, во втором случае силиконовая форма остается на элементе до окончания процесса высыхания.
При помощи вибропресса формируются:
- Блок стеновой цельный;
- Блок стеновой с пустотами усиленный;
- Блок стеновой пустотелый облегченный;
- Половинчатый блок или полублок;
При использовании вибростола и силиконовых форм изготавливаются:
- Блок имитирующий камень;
- Декоративную плитку или элементы для оформления фасада, дорожек, заборов.
Однако сам технологический процесс не будет завершенным без последней стадии, в которой остатки влаги испаряются из бетона, и он постепенно начинает набирать свою прочность. Высыхание играет одну из важных ролей, ведь кроме испарения влаги одновременно происходит и второй не менее важный процесс — поэтапное затвердение цемента.
Для производства в нормальных условиях, высыхание происходит при нормальной температуре с минимальной суточной амплитудой колебания, а для экстремальных условий, например, для температуры ниже +5 градусов Цельсия нужно применять синтетические добавки и присадки для бетона в условиях низких температур.
Для контроля качества и определения готовности блоков к транспортировке и применению в строительстве используют стандартную шкалу набора прочности бетона — 3,5,7 суток форму можно поднимать и переносить, на 9-11 сутки складывать в штабели, на 28 сутки использовать в постройке.
Необходимые материалы
Для строительного материала прочность всегда была одним из наиболее значимых качеств. Но использование только цемента и песка сделает производство бетонных блоков нерентабельным, блоки получаются дорогими.
Выходом из такой ситуации выступает использование в качестве основных материалов для изготовления еще и дополнительных видов сырья как наполнителя. Такие наполнители дают возможность получить продукцию, обладающую дополнительными качествами — легкостью и уменьшенной теплопроводностью.
Для приготовления бетонного раствора используются:
- Цемент марки 400 или 500;
- Натуральный наполнитель;
- Пластификаторы;
- Вода.
Цемент предпочтительнее именно марок 500 и 400, это не только самый популярный, но и наиболее приемлемый для приготовления рецептуры раствора материал. Все рецептуры, рекомендуемые для приготовления бетона основаны на пропорциях именно цемента этой группы.
В качестве наполнителя используется:
- Речной или карьерный песок;
- Щебень гранитный мелкой и средней фракции;
- Гранитный отсев;
- Граншлак;
- Опилки и стружка;
- Керамзит;
- Продукты переработки бетонных изделий и кирпичный бой;
- Химические наполнители, используемые для изготовления утеплителей;
- Доменный шлак.
Приготовление бетонной смеси требует правильной дозировки цемента и пропорций наполнителя. Для качественного бетона стеновых элементов несущих стен берется пропорции:
- Цемент — 1 мерная часть;
- Наполнитель — 7-9 мерных частей;
- Вода — 1\2 мерной части цемента;
Пластификатор, при нормальных температурных условиях, когда температура воздуха стабильно выше +15 градусов не применяется. При понижении температуры, при сушке в неотапливаемых помещениях или на улице добавление пластификатора желательно, но если температура не опустилась ниже +5 его можно и не применять. При температуре ниже +5 такой пластификатор применять обязательно.
Для получения бетона применение пластификатора должно быть максимально точным и дозированным. Большинство производителей добавок рекомендуют делать добавку из расчета 5 грамм на один условный объем формы блока.
Промышленное оборудование
Интенсифицировать производство можно при помощи использования средств малой механизации — электрический вибропресс на 1 форму и бетономешалка на 120-140 литров обеспечит повышение производительности в разы! Правда, здесь придется искать и большую площадку чтобы оборудование для изготовления бетонных блоков можно было использовать на полную.
Для начала успешного бизнеса в производстве строительных материалов нужно не только изготавливать большие объемы продукции, но и предлагать потребителю ассортимент, отличающийся от ассортимента конкурентов. Для этого нужно наладить выпуск материалов для несущих стен, простенков и перегородок, блоков нестандартной формы. Изготавливать такой ассортимент, можно только использовав промышленные образцы оборудования для производства бетонных блоков. В состав установки обычно входит емкость для приготовления раствора, вибропресс и пульт управления. Сама установка делается мобильной, так, чтобы после изготовления одной партии форм она могла переместиться на другое место, чтобы блоки начали сохнуть.
Для мини-завода, применяется оборудование с большей степенью автоматизации и сокращением доли ручного труда. Для линии по производству бетонных блоков необходим миксер для приготовления раствора, формовочные емкости и отдельное помещение с климатическим оборудованием для ускорения процесса сушки. Производительность линии, кроме того потребует еще и линию для упаковки и склад для хранения продукции, готовой к отправке потребителю.
Планируя изготавливать блоки из ячеистого бетона производство нужно дополнить автоклавом, для сушки материала под давлением. Линия в таком случае позволит производить ячеистый бетон специфической формы и назначения, поставляя заказчику готовый комплект блоков для возведения дома или гаража.
Оборудование для самостоятельного изготовления
Самостоятельно изготовить оборудование для приготовления раствора и формовки пустотелого стенового блока в домашних условиях несложно. Достаточно иметь навыки работы со сварочным аппаратом и болгаркой, уметь правильно рассчитать и разрезать металл.
Форма для блока представляет собой правильный прямоугольник с размерами:
- Высота 200 мм;
- Ширина 200 мм;
- Длина 400 мм.
Форма сваривается из листа железа толщиной 4-5 мм. И усиливается снаружи каркасом из уголка или профильной трубы. Для вибропресса для производства бетонных пустотелых блоков лучше использовать сменные элементы для формирования внутренних пустот:
- для несущих конструкций круглые диаметром 100мм;
- для внутренних простенков многопрофильные элементы из квадратной трубы;
- для простенков и полублоков прямоугольные элементы из нескольких профильных труб, сваренных в один элемент.
В качестве вибратора используется стандартный электродвигатель с установленным на вал эксцентриком.
Собранный своими руками вибропрес имеющий привод от электродвигателя обязательно должен быть безопасным от поражения электрическим током — двигатель должен крепиться к корпусу через резиновую прокладку, рукоятки должны иметь резиновые защитные элементы, а используемый кабель двойную изоляцию токопроводящих жил.
betonov.com
Технология изготовления керамзитобетонных блоков
Керамзит, как сыпучий утеплитель, используется не только для проведения теплоизоляционных мероприятий, связанных с утеплением перекрытий. Его нередко используют для производства бетонных блоков, где он выступает в качестве наполнителя. От этого блоки становятся легкими, потому что керамзит в несколько раз легче гравия или щебня, которые он заменяет в керамзитобетонных блоках, плюс уменьшается теплопроводность самого стенового материала. Изготовление керамзитобетонных блоков ничем от обычных бетонных не отличается, главное – точно соблюсти рецептуру используемого раствора.
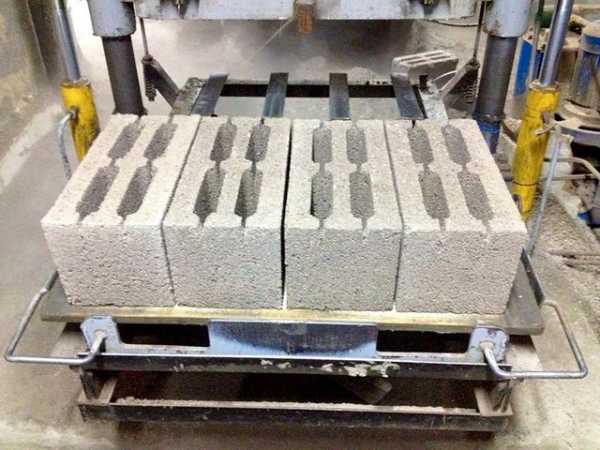
Блоки стеновые из керамзитобетона
Рецептура керамзитобетонного раствора
Обозначим состав керамзитобетона для изготовления блоков из расчета на 1 м³ приготавливаемого раствора.
Материал | Количество, кг |
Цемент марки М400 | 230 |
Песок кварцевый фракции 2-2,5 мм | 600 |
Вода | 190 |
Керамзит (гравий) фракции 5-10 мм | 600-760 |
Вышеобозначенная рецептура соответствует бетону марки М150, что достаточно для сборки стеновых конструкций.
Сегодня большое внимание уделяется такой характеристики, как влагостойкость. Поэтому для производства блоков из керамзитобетона, которые могли спокойно противостоять повышенной влажности и даже прямому воздействию воды (к примеру, косой дождь), в раствор добавляются гидроизоляционные материалы. Один из них – битумная мастика, затворяемая, как 10-процентный водный раствор.
Необходимо отметить, что у такого раствора немного измененная рецептура.
Материал | Количество, кг |
Цемент | 250 |
Керамзитовый гравий | 460 |
Керамзитовый песок (размеры гранул до 5 мм) | 277 |
Вода | 190 |
Битумная эмульсия | 19 |
К производству керамзитобетонных блоков подход разный. Производственная линия с мощным оборудованием и высокой производительностью, где установлены дозаторы, выставленные на пределы веса точно по рецептуре. Второе – ручной способ, где взвешивание компонентов производится чаще ведрами. Поэтому стоит обозначить вес материалов в ведрах (10 л):
- цемент – 13 кг;
- песок – 16;
- вода – 10;
- керамзит (гравий) – 4-4,5;
- керамзит (песок) – 5,5-6.
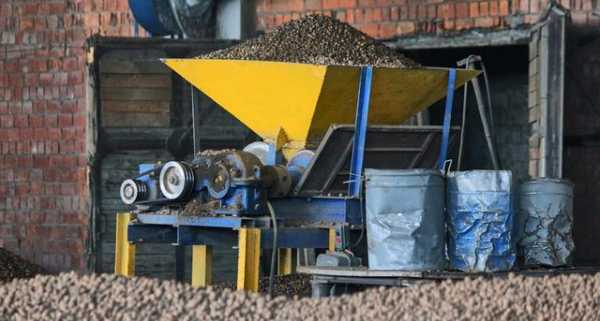
Главное – точная рецептура
Оборудование для производства
Для производства керамзитобетонных блоков (ручным способом) необходимы:
- бетономешалка;
- несколько лопат;
- станок с вибратором;
- несколько форм.
Бетономешалку можно приобрести или взять в аренду. Станки также продаются, хотя это не самое дешевое оборудование. Изготовить их своими руками можно, и если вы неплохой сварщик, то на один станок потребуется один день для сборки. Конструкции станков – огромное количество. В основном это рамные агрегаты, внутрь установлены и жестко закреплены формы. К раме также присоединен жестко вибратор, работающий от сети 220 вольт. Прибор продается в строительных магазинах.
Другой вариант – вибрационный стол, представляющий собой горизонтальную плоскость. Она обычно устанавливается на пружины, к ней же прикрепляется вибратор. Для станка придется изготовить своими руками несколько форм. И чем больше площадь стола, тем больше на нем поместится форм, тем выше производительность самодельного оборудования.
Важно! Не переусердствовать, потому что у вибратора определенная мощность, которой хватает на вибрирование определенной массы.
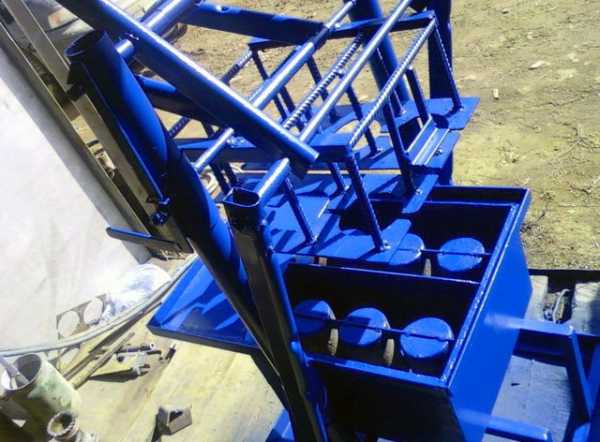
Вибростанок на два блока
Форма для керамзитобетонных блоков
Для изготовления форм используют различные плоские материалы: листовое железо толщиною не менее 2 мм, доски, фанеру, плиты ОСП и прочее. Основная задача производителя работ – подогнать размеры формы под размеры блока: 190х188х390 мм (стандартный несущий стеновой блок). Существуют так называемые полублоки (применяются для возведения перегородок), размеры: 90х188х390.
Стандартные размеры блоков из керамзитобетона
Одна из особенностей керамзитобетонных блоков – пустоты, которые облегчают камень без снижения несущей способности, снижают себестоимость за счет уменьшения используемого объема смеси, увеличивают теплотехнические качества изделия. Поэтому при изготовлении в формы устанавливают жестко три трубы диаметром 40-50 мм, расположенные на одном расстоянии друг от друга и стенками формы.
Трубы соединяются между собой сваркой горизонтальными перемычками (арматура, уголок или стальная лента). К стенкам формы крепятся электросваркой, если форма изготавливается из стального листа, или с помощью саморезов, если применены деревянные изделия.
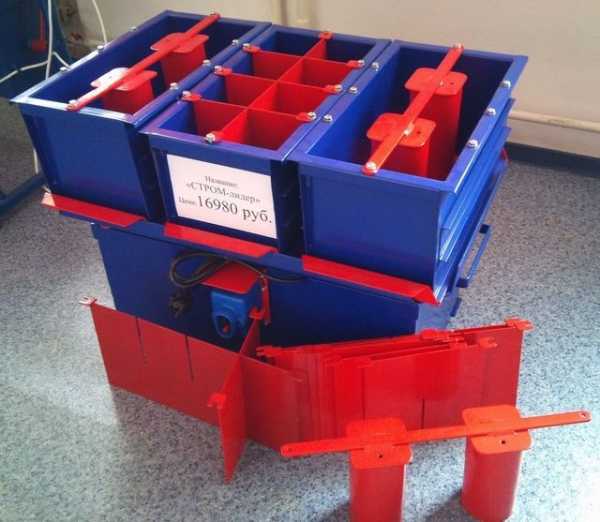
Готовые формы разного вида
Технология производства
Сам технологический процесс проводится в любом помещении с хорошо действующей вентиляционной системой. Размеры помещения зависят от габаритов используемых станков. Керамзитобетонные блоки после изготовления должны пройти процесс сушки, производимую на открытой площадке на улице. Если есть вероятность выпадения атмосферных осадков, то над площадкой лучше возвести навес.
В первую очередь готовится раствор: в бетономешалку засыпается цемент и часть воды. Смесь перемешивается несколько минут до получения однородного состава. Затем в него добавляются порциями песок и керамзит. В конце добавляется оставшаяся часть воды. Конечный раствор должен получиться густым и пластичным.
После чего его из бетономешалки вываливают в подготовленную заранее емкость (корыто), а уже оттуда лопатами перебрасывают в формы, уложенные на вибростол или установленные на вибростанке. Перед этим стенки форм обмазывают отработанным техническим маслом, чтобы блоки легко вышли после затвердевания. Пол вибростола или площадки посыпается мелким песком, чтобы бетон не прилип.
Формы равномерно заполняются раствором, к примеру, пара заброшенных в них лопат смеси. Затем включается вибратор, происходит равномерное распределение бетонного раствора по всему объему формы и его уплотнение. После чего процесс повторяется. Такую процедуру проделывают несколько раз, чтобы заполнить формы полностью. Иногда для придания более точных размеров уложенный и уплотненный раствор дополнительно прижимают сверху металлической крышкой, она на поверхности блока создаст ровную и гладкую поверхность.
В таком виде прямо в формах керамзитоблоки должны простоять не менее суток. После чего их вытаскивают, укладывают на уличную площадку так, чтобы между ними оставался зазор в пределах 2-3 см. Сушиться блоки из керамзитобетона должны 28 суток, что придаст им марочную прочность. Просохнуть материал должен со всех сторон равномерно, поэтому каждый блок в течение сушки переворачивают с боку на бок. Если уложить на сушку их на деревянные поддоны, то переворотами заниматься не надо.
Видео:
Производство блоков из керамзитобетона как бизнес
Начать производить керамзитоблоки, чтобы получать прибыль, не проблема. Главное – все точно просчитать. Как показывает практика, основное требование не к оборудованию, а к размерам помещения и уличной площадке. Чем они больше, тем больше блоков можно уложить на сушку, которая длиться около месяца. Поэтому предлагаются разные варианты проведения сушки. Один из таких показан на фото ниже, где видны специальные стеллажи с укладкой блоков этажами.
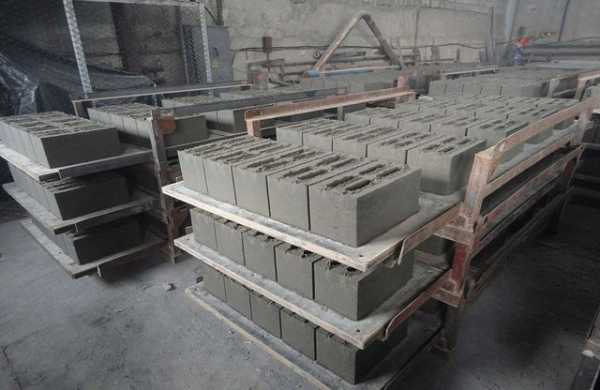
Способ сушки
Все остальное упирается в стоимость сырьевых материалов, которая скачет в зависимости от сезона. Летом цемент стоит всегда выше, потому что спрос на него вырастает за счет увеличения объемов строительства. Особенно это относится к частному сектору.
Поэтому оптимально – производить керамзитоблоки в период осень-весна. Если помещение отапливаемое, то зимой производство не останавливают. Потребление зимой готового стенового материала небольшое, иногда оно сводится к нулю, но летом весь произведенный запас изделий будет распродан. Здесь и надо будет пересчитать его себестоимость по новой цене цемента и других компонентов. Именно здесь кроется большая прибыль.
Кто не первый год в бизнесе такого типа старается все предусмотреть. Кто-то пытается закупить материалы по низкой цене зимой, но есть нюанс – цемент со временем теряет свои свойства, снижается качество. Кто-то, как было описано выше, пытается увеличить производство блоков зимой. В любом случае это прибыльный бизнес пока строительство на пике, пока востребованы строительные материалы. Блоки из керамзитобетона сегодня на пике популярности за счет невысокой цены, высоких теплотехнических качеств и простоты укладки.
viascio.ru
Изготовление строительных бетонных блоков своими руками в домашних условиях
Изготовление строительных бетонных блоков своими руками в домашних условиях
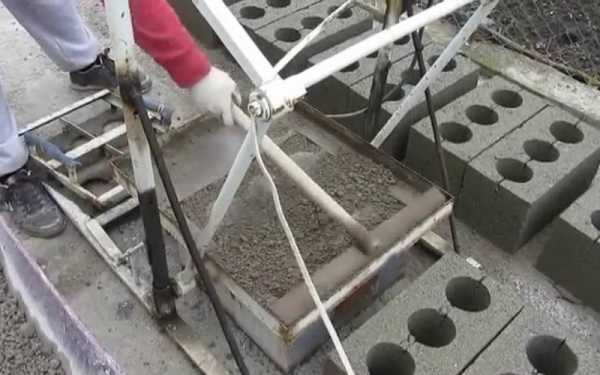
Изготовление строительных бетонных блоков на фото
Для изготовления самодельных блоков требуется лишь несколько форм для их отливки, а также цемент, песок и наполнитель — шлак или битый кирпич. Другие виды наполнителей (гравий или щебень) сделают блок очень тяжелым, а кроме того, стена, сложенная из такого материала, летом будет быстрее нагреваться, а зимой остывать. Если же в качестве наполнителя использовать керамзит, то, хотя он и имеет практически одинаковые теплоизоляционные свойства с битым кирпичом и шлаком, стоить будет в несколько раз дороже.

Формы для изготовление строительных бетонных блоков
Для самостоятельного изготовления строительных блоков в домашних условиях понадобятся специальные металлические или деревянные формы, внутренние размеры которых бывают разными: 150 X 150 х 300 мм, 175 х 175 X 350 мм или 200 х 200 х 400 мм. С небольшими блоками удобнее осуществлять кладку, а с большими быстрее ведется строительство.
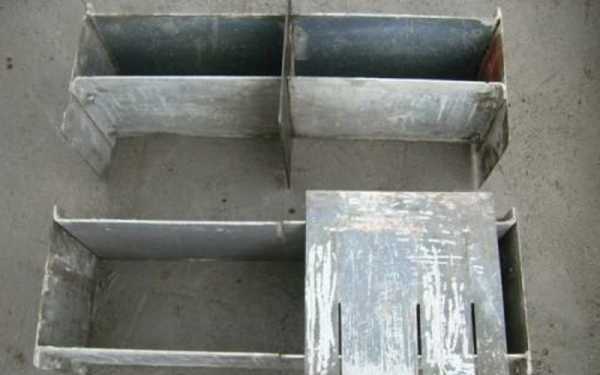
Металлические формы для изготовления строительных бетонных блоков
Для изготовления металлической разборной формы для одного блока потребуется четыре прямоугольные железные пластины толщиной 3-4 мм (высота, ширина и длина пластин будет зависеть от выбранного размера формы). По бокам пластин надо вырезать крепежные пазы, а к торцевым деталям формы приварить ручки. Для формы из четырех блоков потребуется сделать две прямоугольные пластины и пять пластин меньшего размера для разделения будущих блоков в форме.
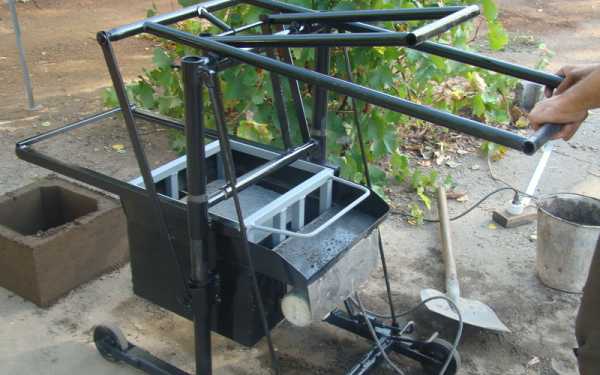
Изготовление строительных бетонных блоков
Для изготовления бетонных блоков своими руками требуется уплотнение и создание в них пузырей, с этой целью надо изготовить специальное приспособление. Для него потребуется одна прямоугольная железная пластина (по размеру формы), небольшой кусок проволоки-катанки сечением 10 мм и три обрезка трубы диаметром 50 мм и длиной 150 мм. На одном конце каждой трубы нужно прорезать по четыре «зуба» треугольной формы на глубину 50 мм. Потом эти зубья надо соединить между собой так, чтобы получился конус. Швы между зубьями необходимо тщательно заварить. Потом к одной из плоскостей пластины нужно приварить ручку из катанки, а к другой — обрезки труб тупым концом.
- Деревянная разборная форма
- Деревянная разборная форма
Для изготовления деревянной разборной формы понадобятся четыре обрезка доски толщиной 35-50 мм (размеры будут зависеть от размеров выбранной формы). Конечно, древесина более слабый материал для формы, поэтому доски нужны качественные и крепкие. Все соединения в деревянной форме надо укреплять с помощью стяжных винтов. В остальном конструкция деревянной формы такая же, как и металлической. Ручки для формы можно сделать из катанки сечением 10 мм, расплющив ее концы и просверлив в них отверстия диаметром 6-8 мм.
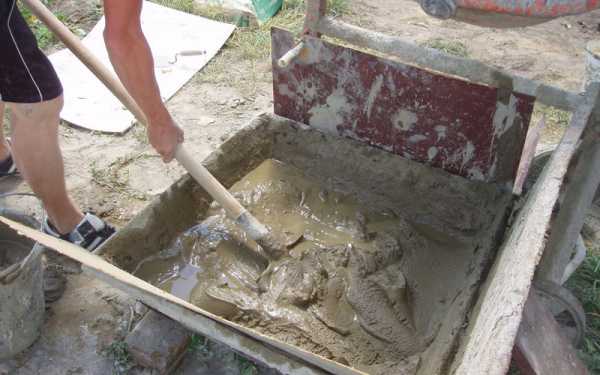
Раствор из цемента для изготовления самодельных блоков
Для изготовления строительных блоков своими руками надо сделать раствор из цемента, песка и заполнителя (шлака или битого кирпича) в соотношении 1:4:6. Добавляя заполнитель в раствор, надо следить за тем, чтобы он был вязким и клейким, но не получился жидким или рассыпчатым. Далее раствор заливается в формы, в которых в жаркую погоду будет застывать в течение 2 ч, а окончательную крепость приобретет через 1-1,5 суток. При прохладной погоде (+7 …+18 С) время затвердевания и полного высыхания увеличивается в 3-5 раз, а при температуре ниже +7 °С и во время осадков блоки делать вообще не рекомендуется.
Если для раствора вместе с цементом будет применяться шлак, можно совсем отказаться от песка, и тогда соотношение цемента и шлака должно быть 1 : 6 или даже 1 : 8.
Перед заливкой раствора в форму надо все ее детали, независимо от материала изготовления, смочить водой. Работать следует на ровной поверхности и заполнять форму раствором на 2/3 или на 3/4 объема (точное количество определяется опытным путем после применения приспособления для проделывания пустот).
После того как блок окончательно застынет, его надо освободить от частей формы. Сырой блок необходимо оставить до полного высыхания, а детали формы залить водой.
Можно делать блоки непосредственно на месте строительства, т. е. выполнять заливку на месте. В этом случае размеры формы для заливки можно увеличить до 330 х 300 х 600 мм. Это еще больше ускорит процесс строительства.
Консистенция цементного раствора и способ заливки такие же, как и в предыдущем случае. Можно сварить в рабочую конструкцию несколько форм (достаточно 3-4 формы), и тогда кладка пойдет еще быстрее.
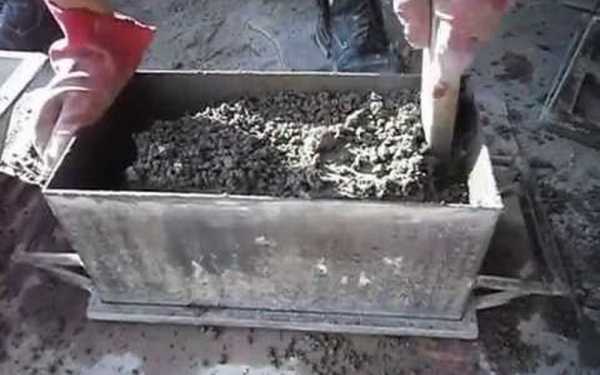
Изготовление строительных бетонных блоков на фото
Чтобы цементная смесь не прилипала к стенкам формы, перед заливкой ее внутреннюю полость нужно обильно смочить водой или смазать отработанным машинным маслом. После схватывания смеси пластины формы отлепляются от стенок блока. В процессе возведения стен надо выверять горизонтальность и вертикальность рядов. В целом кладка углов, перевязь между блоками полностью соответствуют способам кирпичной кладки в полкирпича.
- Саман — смесь глины и соломы, для изготовления самодельных блоков
- Саман — смесь глины и соломы, для изготовления самодельных блоков
Самым дешевым строительным материалом для самостоятельного изготовления бетонных блоков в домашних условиях является саман — смесь глины и соломы. Дешевизна не единственное достоинство самана — это материал прочный, с высокими теплоизоляционными свойствами, простой в «производстве». Для изготовления саманных блоков также используются разборные металлические или деревянные формы. Лучше делать блоки небольшого размера, максимум 150 х 150 х 300 мм, поскольку более крупные блоки тяжелы и неудобны в работе и к тому же в них нельзя проделывать пустоты.
На заметку!
Недостаток самана — неустойчивость к влажности. Перед возведением стен из самана необходимо обеспечить надежную гидроизоляцию фундамента, а готовые стены требуют оштукатуривания цементнопесчаным раствором, покрытия любой доступной полимерной или металлической сеткой и выполнения чистовой отделки.
Домашнее изготовление бетонных блоков для строительства
Порядок работ при строительстве и изготовлении бетонных блоков стандартный: сначала надо выбрать место, потом сделать фундамент — здесь требуется сооружение плиточного фундамента, можно использовать фундаментные плиты, подвести коммуникации, возвести стены, соорудить кровлю, установить окна и двери и выполнить облицовочные работы и оформление интерьера летней кухни.
Стены выкладываются в полкирпича, для летней кухни толщина стены может быть в один кирпич — и этого будет достаточно. По мере кладки необходимо выверять стены по вертикали и горизонтали, используя отвес и шнур, горизонтально натянутый от одного угла домика к другому.
Домашнее изготовление строительных блоков позволяет сокращать затраты на закладку проёмов с последующей установкой окон и дверей. В ходе строительства в коробке здания надо сделать дверные и оконные проемы. Устанавливать место расположения окон и двери надо еще на этапе планирования. Можно в процессе кладки стен в местах установки дверей и окон оставлять проемы нужной ширины, а также вставлять деревянные пробки, к которым потом и будут крепиться коробки-подрамники. Деревянные пробки необходимо вводить во втором ряду относительно нижней части коробки и в предпоследнем ряду относительно ее верхней части. На верхнем уровне коробки следует установить армированную перемычку толщиной 120 мм или брус толщиной 70 мм. Концы перемычки надо завести на стены на 20 см. Если плоскости очередного ряда кладки и верхней части рамы будут находиться на разном уровне, нужно будет догнать их до нужной высоты, используя части блоков и раствор, либо собрать опалубку, связать арматуру и залить цементным раствором.
После возведения стен на отведенные под окна и дверь места следует установить коробки, расклинив предварительно углы. Далее надо выверить их по горизонтали и вертикали и только после этого можно прикрепить боковые части коробки к деревянным пробкам, используя гвозди или шурупы. Оставшееся пространство между стенами, фундаментом, перемычкой и коробкой необходимо заполнить по периметру акриловой монтажной пеной.
Второй способ устройства дверных и оконных проемов — это когда дверные и оконные короба устанавливаются в нужных местах, а затем обкладываются блоками. Обычно такой способ используется при декоративной кладке, когда дальнейшая отделка стен не предусмотрена.
В этом случае, чтобы дверной короб в процессе кладки не повело, нужно по ходу кладки первого ряда зажать его с двух сторон блоками, предварительно вставив в углы подпорки. После второго ряда нужно выровнять короб по вертикали и горизонтали, зафиксировать его гвоздями или шурупами по бокам к стене. Также необходимо оставить выпуск в 10 см. Потом на выпуски нужно нанести раствор и зажать их блоком следующего ряда, еще раз убедившись, что короб стоит ровно. То же самое необходимо проделать и в верхней части дверного короба, а также на четвертом и шестом рядах с коробом окна. Перемычки здесь устанавливаются так же, как при первом способе.
babushkinadacha.ru
Производство керамзитобетонных блоков своими руками и изготовление
Блоки керамзитобетона – это облегченный строительный материал, имеющий высокие показатели прочности, практичности и, главное, возможный к исполнению своими руками. Несмотря на малую массу, модули обладают повышенной плотностью, низкой теплопроводностью, разнообразием модельного ряда. Экологическая чистота материала – еще один плюс модулей, поэтому, если застройщик хочет взять возведение строения в свои руки с самого начала процесса, стоит наладить производство керамзитобетонных блоков у себя на участке. Тем более что изготовление керамзитобетонных блоков потребует небольших финансовых вложений, а себестоимость модуля окажется значительно ниже, чем покупать готовый продукт у производителя.
Оборудование для производства модулей
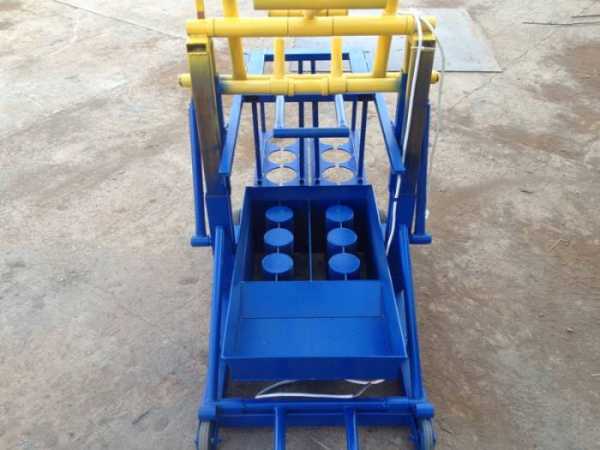
Чтобы делать керамзитобетонные блоки своими руками, необходимо приобрести, взять в аренду или сделать соответствующее оборудование
Чтобы делать керамзитобетонные блоки своими руками, необходимо приобрести, взять в аренду или сделать соответствующее оборудование, а также купить качественное сырье. И тут дешевиться не стоит – чем более высокого качества окажется исходный материал, тем более прочными и практичными получатся модули. Для облегчения процесса и наладки линии по производству керамзитобетонных блоков в нужном для застройщика количестве, потребуется следующее оборудование:
- Вибростол;
- Бетономешалка;
- Формовочные металлические поддоны.
Если позволяют финансы, неплохо приобрести установку вибропрессовочного типа, она заменит два прибора: формы и вибростол. Также необходимо подобрать хорошее помещение с ровным полом и определить место для сушки модулей.
Важно! Вибростолы различаются по маркам и производительности: некоторые из них выпускают до 120 модулей в час, а некоторые до 70 единиц продукции. Для частного пользования вполне подойдут малоформатные станки мощностью до 0,6 кВт и производительностью до 20 блоков/час. Ценовая градация в пределах $ 30 – это идеальные по своим компактным размерам приборы, используемые для производства керамзитобетонных блоков своими руками в частном домостроении.
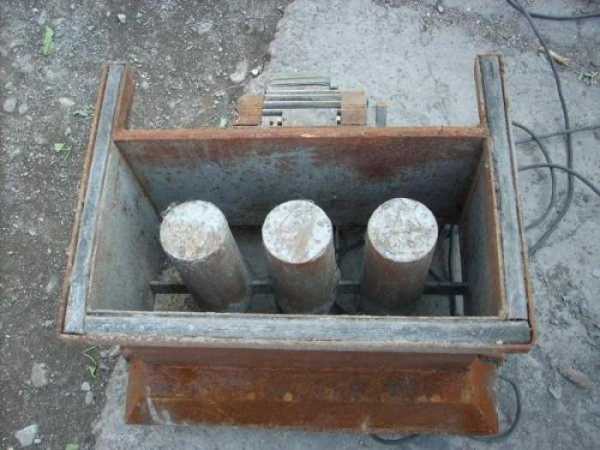
Изготовление станка для производства керамзитобетонных блоков собственными силами также возможно
Изготовление станка для производства керамзитобетонных блоков собственными силами также возможно. При небольшой сноровке и малых навыках, прибор получится ничуть не хуже, чем фабричный, однако цена его будет в 10 раз ниже. Предлагаем вариант самого простого оборудования для производства керамзитобетонных блоков типа «несушка» — это агрегат, оснащенный формовочным ящиком без дна, вибратором, располагающимся на боковой стенке и ручками для демонтажа матрицы.
Важно! Стандартные габариты одного блока составляют 390*190*188 мм, допустимый процент пустотности не более 30%, причем щели могут иметь как круглую, так и продолговатую форму – важно лишь то, чтобы пустотообразователь был выполнен в форме конуса, для облегчения снятия формовочной коробки с готового блока.
Для изготовления матрицы потребуется лист металла толщины 3-5 мм, из которого нужно вырезать заготовку с запасом в 5 см для процесса утрамбовки смеси. Формовка изготавливается в виде сквозного ящика без дна. Сварной шов должен остаться снаружи, иначе он испортит форму модуля.
Рекомендуем к прочтению:
Для устойчивости станка, по бокам прибора приваривают планки из профильных тонких труб, а по периметру оснастить конструкцию резиновой обивкой. Неплохо оснастить всю систему фартуком для того, чтобы раствор не просыпался. А вот вибратор выполняется из движка старой стиралки мощности 150 Вт (это можно сделать, сместив центры). На вал крепится металлическая планка с краевым отверстием – эксцентрик, параметры которой определить лучше пробным путем. Если остались вопросы, как выполнить станок для изготовления модулей, смотрите видео – ответы будут полными и подробными.
Подготовка и процесс производства модулей из керамзитобетона своими руками
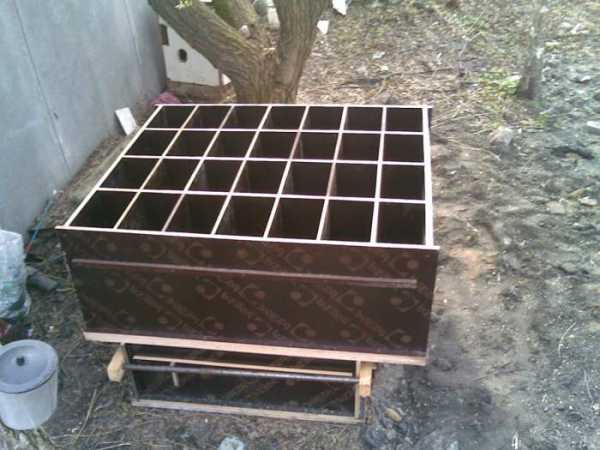
Чтобы приготовить смесь и блоки, потребуется форма с гладкой поверхностью
Чтобы приготовить смесь и блоки, потребуется форма с гладкой поверхностью. Допускается исполнение заготовок как из металлического листа, так и из досок – в этом случае готовый модуль получится фактурным. Сам процесс включает 4 этапа:
- Смешивание ингредиентов строго по рецептуре. В частности, песок составляет 3 части от всего объема смеси, вода – 0,8-1 часть, как и цемент, а вот керамзита брать уже 6 частей. Важно не только соблюсти рецептурную технологию производства керамзитобетонных блоков, но и правильно смешать компоненты: сначала в бетономешалку помещается вода, керамзит, потом цемент и песок. При использовании дополнительных компонентов, их также загружают в емкость бетономешалки.
- После промесса наступает этап формовки. Применение вибростанка ускорит процесс: в формовку, куда предварительно уложена пластина, помещается смесь, включается движок для вибрации и убираются излишки состава.
- Пластину с готовой формой поднять посредством рукояток, получится полноценный модуль, который отправляется на сушку.
- Просушивание длится не менее 48 часов, при этом заготовки должны быть защищены от солнца, дождя. После высыхания с модулей снимаются пластины.
Это самый быстрый процесс, при котором изготовление керамзитобетонных блоков в домашних условиях не доставляет проблем. Однако если нужно сделать керамзитобетонные блоки своими руками более прочные и плотные, имеет смысл добавить процесс пропарки, тогда материал наберет повышенную крепость и время набора бетоном марочной прочности сократится до 28 суток.
Варианты составов смеси бывают разные, однако песок, вода, цемент и керамзит – основные компоненты. В качестве дополнения можно добавить омыленные древесные смолы, увеличивающие морозостойкие качества материала и лигиносульфонат технический, повышающий связанность смеси.
А теперь чуть подробнее о том, как сделать керамзитобетонные блоки самостоятельно:
Рекомендуем к прочтению:
- Чтобы приготовить раствор, пропорции и ингредиенты такие:
- Портландцемент М400 или шлакопортландцемент – 1 часть;
- Керамзитовый гравий – 8 частей;
- Чистый кварцевый песок – 2 части и 3 части для фактурного слоя;
- Воды чистой – расчет 225 л на 1м3 смеси.
Совет! Чтобы придать пластичность, неплохо добавить ложку обычного стирального порошка или мыльного состава для мытья посуды.
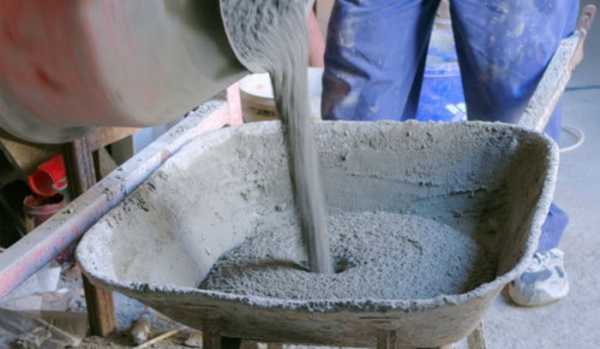
Варианты составов смеси бывают разные, однако песок, вода, цемент и керамзит – основные компоненты
- Все ингредиенты всыпаются в бетономешалку, причем тут следует сначала высыпать сухие компоненты, а только затем влить воду. Если соблюдены пропорции, то масса по консистенции будет похожа на пластилин.
Совет! Получаемый блок будет весить примерно 16-17 кг. При этом форма заготовки допускается как стандартных размеров, так и произвольных: 390*190*14, 190*190*140 и других.
- Формовки устанавливаются на ровную поверхность, изнутри стенки заготовки обильно смазываются машинным маслом, а основание посыпается песком.
- Заполнить формы смесью, утрамбовать на вибростоле или применить для этого деревянный брусок. Трамбование ведется до тех пор, пока не образуется цементное молочко. После этого выравнивается поверхность, и заготовки отправляются на сушку.
Важно! Опалубка снимается не ранее, чем через сутки! Важно уберегать заготовки от прямых лучей солнца, так как неравномерность просушки приводит к растрескиванию поверхности модулей.
Как видите, купить, сделать оборудование для производства блоков керамзитобетона дома и выполнить все процессы несложно. А вот изготовленные таким образом модули будут ничуть не хуже заводских.
Рассчитываем себестоимость
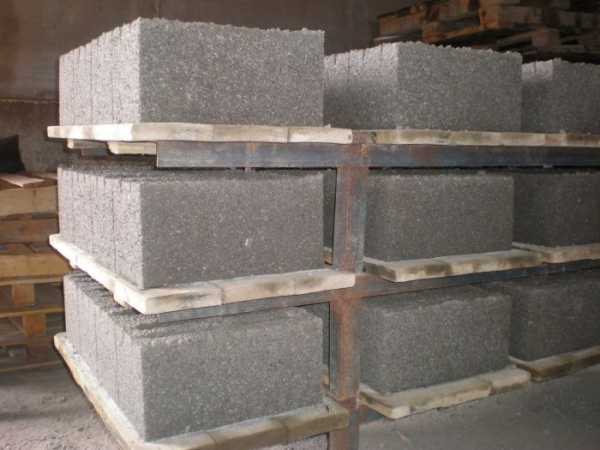
Все работы требуют предварительных подсчетов, иначе и не стоит начинать производство керамзитобетонных блоков
Все работы требуют предварительных подсчетов, иначе и не стоит начинать производство керамзитобетонных блоков дома своими руками. Чтобы подсчитать себестоимость, придется точно вызнать цену составляющих и понять, во сколько обойдется единица готового материала. В частности, рассматривая стандартный модуль 390*190*140 мм, получается объем раствора 14 литров. Вычитываем пустотообразователи, которых, как правило, не более 25-30% итог равен 11 литрам смеси. Теперь просчет компонентов:
- На одну штуку уходит 0,005 куба песка, которым заполняется 5 л всего объема;
- Керамзита примерно требуется столько же, как и песка;
- Цемента потребуется 1,25 кг.
Осталось выяснить цену на ингредиенты, учесть воду, другие компоненты и просчитать себестоимость единицы модуля. По самым примерным расчетам она составит до $ 5. Как видите, цена невероятно мала. Однако, для полной картины не хватает подсчета затрат на оборудование, трудовые затраты и временные, которые любой застройщик обязан включать в подсчеты. Но и при таком полном раскладе, стоимость блочных модулей, из которых получатся отличные стены из керамзитобетонных блоков, выполненных своими руками, все равно ниже, чем от завода-производителя. Поэтому, если вы планируете ставить свой дом на участке, смотрите еще раз технологию изготовления материала, видео от профессионалов и начинайте планировать процесс запуска производства керамзитобетонных блоков у себя на участке – это выгодно, практично и доступно для каждого мастера.
kakpostroitdomic.ru
Производство бетонных блоков
Производство бетонных блоков – основные варианты технологии
Самые разнообразные изделия из бетона широко используются как в промышленном, так и в частном строительстве. При этом одним из самых главных достоинств является тот фактор, что блоки можно изготовить и своими руками – оборудование для производства бетонных блоков отличается простотой, установки для пенобетонных изделий несколько сложнее, но, тем не менее, их стоимость также достаточно демократична. Освоить все особенности работ не составит большого труда, главное – соблюдать требования технологии.
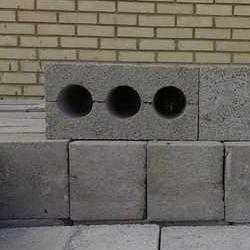
На фото: блоки из бетона, изготовленные самостоятельно, практически не уступают заводским вариантам
Преимущества самостоятельного изготовления блоков
Конечно же, купить готовые изделия гораздо проще, но и у варианта с самостоятельным производством есть свои плюсы:
Цена | Стоимость одного изделия при его изготовлении своими руками получается примерно наполовину ниже. Это особенно важный фактор при нехватке средств, ведь можно провести работы со значительной экономией, хотя это и более трудозатратный вариант |
Качество | Вы точно можете быть уверены, что при изготовлении применялись только качественные компоненты и соблюдались все требования технологии. Очень часто недобросовестные производители продают некачественные изделия, что сказывается на прочности построек |
Соответствие требованиям | Этот пункт особенно актуален, если вам нужны блоки нестандартных размеров. Вы можете самостоятельно изготовить форму любого размера, что сразу же решает любые вопросы по параметрам изделий |
Возможность заработать | Изготовление блоков самостоятельно может не только обеспечить вас строительным материалом, вы можете делать продукцию на продажу. Опять же, средства можно вкладывать в собственную стройку |
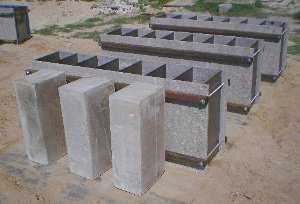
Пенобетонные блоки изготовить гораздо проще, чем кажется на первый взгляд
Особенности технологии
Сразу стоит отметить, что можно проводить два основных варианта работ: изготавливать бетонные с наполнителями или пенобетонные изделия. Обе технологии имеют кардинальные отличия, поэтому мы подробнее рассмотрим каждый из вариантов.
Бетонные блоки с наполнителем
Оборудование для производства бетонных блоков отличается простотой, вам понадобится бетономешалка, формы и вибростол. Причем в самом крайнем случае можно обойтись только формой, но от этого качество несколько снизится.
Сам процесс достаточно прост:
- В первую очередь необходимо подготовить компоненты – песок, цемент, наполнитель (это может быть щебень, шлак, керамзит и многое другое, все зависит от того, какой компонент доступен в вашей местности).
Важно! Правильная консистенция раствора – он должен при сжатии в руке образовывать комок, который при падении на землю разбивается. Такой состав оптимален для производства бетонных блоков.
- Далее стоит определиться с оптимальным размером форм, самый популярный вариант – 20х20х40, при этом стоит помнить, что в процессе работы часто нужны и половинчатые элементы, поэтому форма 20х20х20 также будет очень актуальной. Для изготовления можно использовать металл либо дерево (если применяется дерево, то с внутренней стороны форму лучше всего отделать жестью для идеальной гладкости будущих изделий).
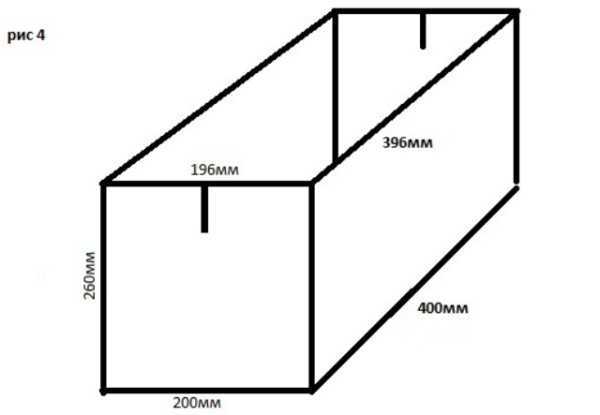
Форма может быть изготовлена из чего угодно, главное – чтобы материалы были плотными
- Для того чтобы изделия проще доставались из форм, все элементы, соприкасающиеся с бетоном, смазываются специальной смазкой либо машинным маслом (подойдет и отработка, это абсолютно не принципиально).
- Установка для производства бетонных блоков представляет собой вибростол, уплотняющий смесь. Как отмечалось, можно работать и без него, но будет страдать качество, поэтому лучше изготовить простейшее приспособление или поступить так: взять оборудование напрокат на несколько дней.
- Инструкция по изготовлению достаточно проста: готовится раствор, после чего форма заполняется и уплотняется каким-либо способом. Если в изделии нужны пустоты, можно воспользоваться бутылками, которые также необходимо смазать. Вынимать блоки можно через 1-2 дня, после чего производится сушка в течение как минимум 2-х, а лучше 4-х недель.
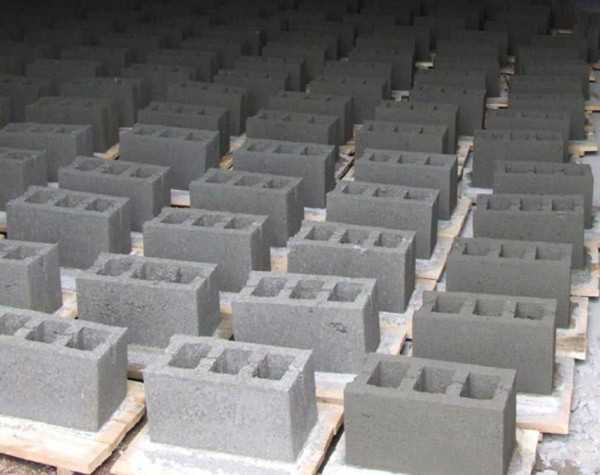
Сушка – ответственный этап работ
Пенобетонные изделия
Технологическая схема производства пенобетонных блоков отличается от обычных изделий:
- Основными компонентами являются цемент, песок и специальный состав для создания пены. В этом случае главное значение имеет обеспечение стойкости образовавшейся пены и ее равномерное распределение по структуре изделий, именно поэтому важно использовать хорошую установку. Самым простым и эффективным вариантом на сегодняшний день является использование бароустановок, они обеспечивают хорошее качество изделий и стоят достаточно мало.
Оборудование для производства пенобетонных блоков отличается компактностью и простотой эксплуатации – особенности работы можно освоить за очень короткое время
- Процесс довольно прост: в оборудование подается необходимое количество компонентов, и в течение нескольких минут производится приготовление состава, который затем можно заливать в формы, а можно заполнять опалубку и создавать монолитные конструкции.
Совет! Такой вариант отлично подходит для заполнения полостей – состав заполнит все пустоты между стенами и после застывания обеспечит отличную теплоизоляцию.
Это отличный вариант для собственного бизнеса – производство пенобетонных блоков отличается высокой окупаемостью, и вы сможете выйти на прибыль уже через 3 месяца нормальной работы.
Мобильная установка позволяет изготавливать пенобетон в нужном месте
Вывод
Изготовл
vest-beton.ru
Производство строительных блоков | Полезное своими руками
В сельском строительстве сегодня довольно успешно применяются детали из железобетона, которые по существу заменили незаслуженно забываемые, но испокон веков применяемые местные материалы. А ведь из местных материалов на селе возводили, да и сейчас возводят прочные, красивые, теплые, долговечные и абсолютно экологически чистые жилые дома и другие постройки.
В этой статье я хотел бы рассказать вам об одном хорошо известном и проверенные способе изготовления строительных материалов (в частности кирпича) в сочетании с новыми приемами, технологиями и техникой. Это сочетание позволяет повысить качество строительных материалов домашнего изготовления, а также механизировать их производство, сделать их более доступными и дешевыми.
Рекомендации, приведенные в данной статье, предназначены для людей, испытывающих затруднения со строительными материалами для собственных нужд при строительстве дома, дачи, гаража, а также других построек фермерско-хуторского, единоличного, семейного или коллективного хозяйства, а также для предпринимателей малого бизнеса, собирающихся заняться строительными работами или производством строительных материалов.
Прямое безобжиговое прессование
Прямое безобжиговое прессование кирпичей, плиток и строительных блоков — экологически абсолютно чистое производство. Таким путем можно получить строительные материалы различных назначений: стройблок, кирпич, дорожный камень (брусчатку), черепицу, облицовочную и тротуарную плитку.
Качество изделий зависит только от качества изготовления пуансона и матрицы: поверхность может получаться глянцевая, прочность — в зависимости от количества и качества связующего, вводимого в смесь, — до 600 кг/см2.
Получение материалов с более высокой прочностью здесь не рассматривается ввиду их неэкономичности и сложности технологии производства.
При строительстве одно-двухэтажных зданий и сооружений вполне достаточно прочности кирпича марки М30. Расчеты показывают, что марка М20 должна держать на себе столб кладки (теоретически) до 80 м высоты, но с учетом неоднородности прочности кладки, устойчивости и запаса прочности, принято вполне безопасным строительство зданий до двух этажей при кладке стен толщиной 45 см. При строительстве, трехэтажных зданий необходимо увеличить толщину стен первого этажа до 66 см.
Условием прямого безобжигового прессования строительных изделий является минимальное количество влаги и большое предварительное обжатие. Полная естественная сушка заканчивается через неделю.
При минимально необходимом количестве влаги в смеси, с использованием связующего цемента и предварительном обжатии до 5 кг/см², готовые изделия имеют способность к самопрогреванию, в результате чего сушка проходит более интенсивно, и уже через сутки изделие созревает для использования его в кладке.
Расход вяжущих материалов (цемент, известь) при получении строительных материалов методом прямого прессования полусухой смеси вдвое ниже, чем при вибрационной формовке, а в большинстве случаев можно обойтись и без них. (При вибрационной формовке бетонная смесь должна иметь достаточное количество воды, иначе будет недостаточной ее подвижность. Однако излишнее количество воды уменьшает конечную прочность изделий.)
Известны два вида блоков с использованием в качестве связующего цемента:
- Бетонные изделия. Их можно изготовить по самому экономному в отношении цемента рецепту для прямого прессования по рекомендации фирмы «Интерблок», завоевавшей популярность своей «сухой кладкой». Для этого надо смешать 10 частей мелкого щебня, 6 частей песка и 1 часть цемента М400. Такие изделия будут готовы к укладке через сутки сушки при плюсовой температуре. Прочность — 30 кг/см². Их можно использовать в нулевом цикле: для фундамента, цокольной части, мощения дорог, изготовления бордюров и т. п.
- Цементно-песчаная плитка (блок). Ее можно изготовить, смешав 10 частей песка, 1 — 3 части цемента. Количество цемента (он берется марки М300 — М400) зависит только от необходимой конечной прочности и его марки. Для изготовления защитного слоя желательно придерживаться соотношения 10:2.
Бесцементные грунтовые блоки (терраблоки)
Их делают из грунтов с содержанием глины в них не более 10 — 15%. Непригодны для изготовления терраблоков — растительный слой и заиленные грунты.
Как отличить тощую глину от жирной, а также достоверно определить качественный состав глины, вы можете узнать прочитав эту статью.При использовании тощих (с незначительным содержанием глины) грунтов в них добавляют глину.
Приготовленная смесь должна иметь такую влажность, чтоб сжатая в кулаке горсть смеси схватывалась в комок, но не пачкала рук.
При использовании жирных (с большим содержанием глины) грунтов в них добавляют песок, золу, шлак.
Пригодность применяемого грунта определяют по-разному. Если, например, откосы и стенки канав или глубокие колеи на грунтовых дорогах, не обросшие травой, не осыпаются, такой грунт пригоден для возведения стен или изготовления стеновых блоков.
Если пешеходные дороги не размываются дождем или комья земли не распадаются на лопате, это свидетельствует о пригодности грунта.
Но грунт можно испытывать и так. Берут ведро без дна, ставят на ровный пол или ровную прочную подкладку. В ведро насыпают грунт слоями по 10 — 12 см, причем каждый слой трамбуют до тех пор, пока трамбовка не станет отскакивать.
Наполнив таким образом ведро грунтом, его поднимают и опрокидывают на ровную доску. Полученный конус предохраняют от дождя, ветра и солнца в течение 8-12 суток. Если после этого конус, падая с метровой высоты, не разобьется, это свидетельствует о высоком качестве грунта.
Образование трещин говорит о том, что грунт жирный. Если блок рассыпается — грунт тощий.
Не волнуйтесь — все легко корректируется. К жирному грунту добавляют тощий или песок, золу, шлак, костру, соломенную сечку, стружку, камышовую мелочь. К тощему грунту добавляют глину. Небольшое количество мелких камней, щебня и органических примесей (до 30%) не снижает качества блоков.
Для облегчения грунта и снижения его теплопроводности можно добавлять утеплитель — волокнистые добавки. Можно применять и лессовидные грунты, но обязательно добавляя в них до 40% мелкого шлака или до 15% извести-пушонки.
При добавлении извести первоначальная прочность материала через 20 — 30 лет повышается с 15 до 100 — 120 кг/см2.
Терраблоки, изготовляемые по вышеуказанным рекомендациям, должны пройти естественную сушку. Через две недели такой сушки их прочность будет более 15 — 20 кг/см2, но останется чувствительность к воздействию влаги. Такие блоки лучше использовать в перегородках.
Для повышения прочности и влагостойкости в сырьевую смесь можно вводить добавки: 3 — 8% низкомарочного цемента или 15 — 20% извести-пушонки, или 70 — 90% кг/м3 торфяной крошки на 1 м3 грунта. Торфяная крошка увеличивает влагостойкость в 10 раз, при этом прочность блоков не уменьшается.
Добавка цемента в смесь может дать прирост прочности сразу в три раза. При добавлении цементов грунтомассу необходимо использовать не позднее чем через час после ее приготовления.
Самые лучшие результаты (в экономии вяжущих материалов) при использовании прямого прессования дают добавки в сырьевую смесь цемента низкомарочного 2-4% или извести 5-7%. Следует иметь в виду, что использование низкомарочного цемента при прибавлении смесей более оправдано по экономическим и технологическим соображениям.
При использовании цемента марки М300 и выше желательно понизить его марку до М150 и ниже путем разбавления его со шлаковой пылью, печной золой или песком при равномерном распределении его в смеси. Шлаковую пыль лучше брать от электрофильтров — она обладает малыми связывающими свойствами и может вполне заменить цемент; при этом достаточно разбавлять его в 2-3 раза больше, чем низкомарочного цемента.
Несколько слов о содержании воды
При технологии прямого прессования приготовленная смесь должна иметь влажность 6-8%, несмотря на ее состав.
Верный признак оптимальной влажности: сжатый комок в кулаке не пачкается и не рассыпается.
При большой влажности смесь смешивается с более сухой такого же состава, с последующим перемешиванием до однородного состояния. Вода не добавляется: влаги достаточно в глине и грунте.
Саманные блоки
Их готовят аналогично грунтовым и можно использовать все рекомендации, связанные с изготовлением терраблоков, особенно по применению добавок цемента или извести.
Отличие от терраблоков только по составу исходной смеси. Саман готовят из глины, песка с примесью волокнистых добавок (соломенной сечки, костры, мха, стружки, камышовой мелочи и др.).
Состав самана зависит от жирной глины: на 1-2 части очень жирной глины — 1 часть песка и 11-14 кг волокнистых добавок.
Корректировку жирности можно производить и за счет изменения количества песка.
Для приготовления самана сначала смешивают глину с песком до получения однородной массы. Соломенную сечку предварительно смачивают водой. Добавляя ее в массу, все тщательно перемешивают.
Качество глины повышается, если ее заготовить осенью и уложить на открытом месте валом высотой до 1 м. Напитавшись водой осенью, глина зимой промерзает, вспучивается и разрыхляется.
Свежевскрытая глина также обладает хорошими качествами.
Чтобы глина, заготовленная впрок, не усыхала, ее лучше покрыть камышовыми или иными матами или соломкой, изредка поливая маты водой.
«Саман-сэндвич» и «терра-сэндвич»
Они отличаются от обычных блоков тем, что имеют защитный облицовочный слой большей механической прочности и влагостойкости, чем основной.
Защитный слой с добавками красящих наполнителей может иметь также высокие декоративные качества: можно получать блоки с защитным слоем всех необходимых цветов.
На защитный слой можно наносить и орнаменты печатной технологией. Кладка из цветных блоков и блоков с печатными орнаментами создает неповторимый колорит постройки.
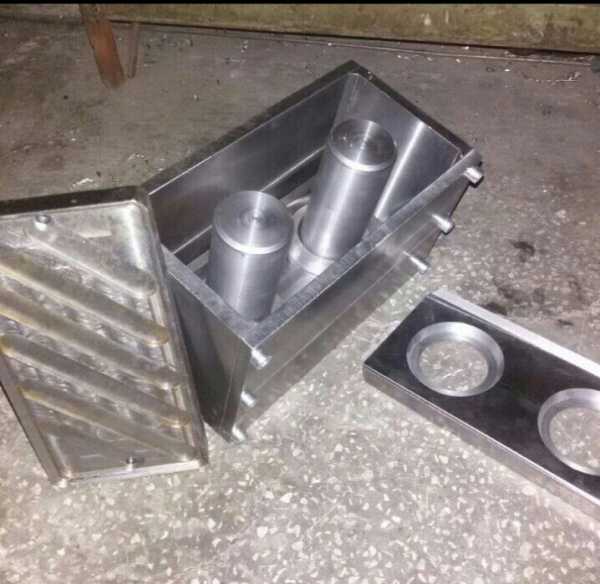
electro-shema.ru
Производство керамзитобетонных блоков: технология
Керамзитобетонные блоки — легкий стройматериал, который применяется для кладки стен. Продукцию, представленную на рынке, как правило, изготавливает тот или иной завод керамзитобетонных изделий (в частности, алексинский). Также можно приобрести товары компании Еврокам и блоки, выпущенные на заводе керамзитового гравия (Винзили). Несмотря на то, что керамзитобетон имеет сравнительно небольшой вес, он обладает достаточной прочностью. Кроме того, керамзитобетонная поверхность не вредит окружающей среде, а изготовить такой блок можно и в домашних условиях. Технология производства изделий позволяет в значительной степени сократить финансовые затраты. Качество керамзитобетонных блоков будет высоким, если при их производстве применять хорошие материалы.
Технология изготовления
При строительстве малоэтажных строений специалисты часто возводят стены из керамзитобетонного блока. Применение этих стройматериалов обещает большую выгоду, нежели приобретение кирпичей, поскольку блокам свойственны несколько преимуществ. Прежде всего, на кладку керамзитоблоков потребуется меньшее количество времени и цементной смеси. Помимо этого, теплопроводность блоков считается низкой, за счет чего изделия обладают высокой теплоизоляцией. При этом производство керамзитобетонных блоков — несложный процесс. Технология создания керамзитобетонной смеси компании Еврокам схожа с методами изготовления аналогичных стройматериалов. Если есть такая необходимость, то можно сделать раствор своими руками или приобрести материалы, сделанные на заводах Алексина или керамзитового гравия (Винзили). Завод керамзитобетонных изделий выпускает качественную продукцию. Для этого нужно только соблюдать технологию и пропорции компонентов. Перед началом работ важно заранее узнать о преимуществах и недостатках керамзитобетона. Процесс делится на несколько этапов:
- Подготовка оборудования. Технология изготовления изделий предполагает использование специального оборудования. Вам понадобится бетономешалка и вибростанок. Предварительно необходимо расспросить у специалистов об особенностях работы вибростанка. Вместо него можно воспользоваться вибростолом. Стоимость оборудования может быть высокой, но качество на выходе оправдывает такие затраты. При этом его применение предполагает создание одного либо нескольких изделий. Но важно учитывать, что использование оборудования рассчитано и на физический труд рабочих. Вибростанки — сложный механизм, но работать с ними просто даже новичкам. На них необходимо закрепить блок-форму, на которую будет передаваться вибрация. За счет пуансона получаются блоки с гладкой поверхностью. Создание изделий осуществляется при помощи вибропресса, который вмонтирован в станок.
- Подготовка строительных материалов. Прежде всего, необходимо подготовить помещение с хорошей вентиляцией. Кроме того, понадобится уличная площадка для сушки и последующего хранения стройматериалов. В состав блоков из керамзитобетона входит несколько компонентов. Речь идет в первую очередь о главном материале — керамзите. В роли вяжущих веществ выступают цемент (М400), мелкий песок и жидкость. Эти ингредиенты – обязательные компоненты бетонной смеси. Керамзит также должен быть мелким, поскольку такая форма материала является наиболее подходящей для подобных изделий. Чтобы осуществить производство высококачественных и прочных блоков, понадобится приобрести специальные добавки. Для большей морозостойкости в состав подмешивают омыленную смолу деревьев, а для повышения связывания — лигносульфонат. Пластичность материала поможет увеличить стиральный порошок. Необходимо добавить в цементный раствор одну ч. л. на ведро жидкости.
Смешивание компонентов. Бетонную смесь следует изготавливать в бетономешалке. Во время проведения работ важно соблюдать указанные пропорции. Так, цемент должен составлять одну часть, измельченный керамзит — шесть частей, песок — три части, вода — одну.. Чтобы правильно изготовить раствор, внутрь бетономешалки нужно налить жидкость, затем засыпать керамзитовый песок. После впитывания воды в состав можно добавить цементную смесь и мелкий песок. Перемешивание раствора длится примерно две минуты. Необходимо, чтобы консистенция керамзитобетона была однородной.
- Формовка. Следующий этап производства блоков из керамзитобетона – формовка при помощи вибростенда. В углубление установки следует поместить подготовленную смесь, затем включить оборудование. Вибрация поможет ликвидировать пустоты в растворе, одновременно повысив его плотность. После этого смесь можно распределять в формы. Чтобы покрытие получилось максимально ровным, нужно убрать все излишки с поверхности. Завершив этот этап, вы можете начать сушку блоков.
- Сушка. Этот шаг является последним в изготовлении керамзитоблоков. Закончив заливку изделий, рабочие должны оставить блоки, по меньшей мере, на сутки (лучше — на двое). Затем следует разобрать специальные формы, положить блоки на открытую площадку и укрыть изделия от осадков и попадания сора. Сушка длится примерно двадцать восемь дней. Затвердевший керамзитобетон можно применять для укладки стенок.
Укладка
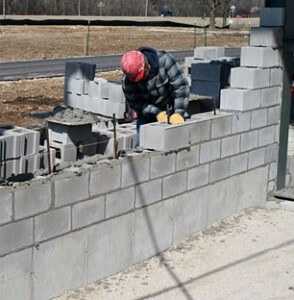
Так как первая линия кладки является основой здания, блоки нужно распределять особенно тщательно и аккуратно. После укладки каждых двух-трех керамзитоблоков нужно проверять, насколько ровной получается кладка. Для этого вам понадобится строительный уровень. Затем следует замазать щели цементным раствором. Каждый последующий слой укладывают таким же образом. Также важно помнить, что швы не должны слишком выделяться. Вместе с тем необходимо, чтобы они надежно удерживали остальные блоки. Так, ширина швов может составлять примерно полтора сантиметра.
Специалисты отмечают, что нельзя заполнять смесью отверстия, имеющиеся внутри керамзитоблоков. Во-первых, вы израсходуете на это большое количество цемента, во-вторых, блоки потеряют изоляционные характеристики. Кроме того, стоит принимать во внимание то, как вы будете отделывать стену. Например, если планируется облицовывать керамзитоблоки кирпичами, можно не заниматься дополнительной отделкой стены. А если вы не намерены облицовывать поверхности, то сделайте «расшивку».
Вернуться к оглавлениюХранение и транспортировка материалов
Керамзитоблоки поставляют на специальных европоддонах, защищают от неблагоприятных воздействий при помощи пленки из полиэтилена. Пакеты можно перевозить любым видом автотранспорта, согласно утвержденным правилам транспортировки грузов. Стройматериалы разгружают всеми способами, которые гарантируют сохранность изделий и не нарушают технику безопасности. На стройплощадке такие поддоны устанавливают горизонтально. Хранить блоки нужно в помещениях с низким уровнем влажности. Важно, чтобы на блоки из керамзитобетона не попадала влага. Керамзитоблоки обычно складируют на специальные поддоны. Они должны находиться под навесом, быть укрыты брезентом.
Соблюдение условий хранения и перевозки поможет сохранить качество продукции.
kladembeton.ru