Технология производства пенополистирола из вспенивающегося полистирола.
Технология производства пенополистирола из вспенивающегося полистирола
1. Физико-химическая последовательность процесса.
Процесс производства пенопласта из вспенивающегося полистирола складывается из четырех
последовательных технологических операций.
А. Первоначального производства гранул из вспенивающегося полистирола
Б. Выдержки по времени вспененных гранул из вспенивающегося полистирола
В. Формирование блоков из вспенивающегося полистирола
Г. Сушка и выдержка по времени блоков из вспенивающегося полистирола.
А. Процесс производства гранул, происходящий во вспенивателе с помощью водяного пара, происходит при температуре 80-100 градусов Цельсия. Благодаря содержащемуся в гранулах порофору (обычно пентан, изопентан или пентан-изопентановая фракция), повышенной температуре и расширению водяного пара, гранулы многократно увеличивают свой объем и принимают микроячеистую структуру.
Б. Во время выдержки по времени вспененных гранул из полистирола происходит процесс диффузии воздуха вовнутрь микро ячеек и выравнивание давления внутри ячеек и атмосферным давлением.
В. Процесс формирования блоков из вспенивающегося полистирола, происходящий в закрытых формах, заключается в нагревании водяным паром вспененных и выдержанных гранул. Благодаря повышению температуры, а также заключенному в порах гранул порофору, воздуху и водяному пару, наступает дальнейшее расширение объема гранул и их взаимное слипание, приводящее к возникновению монолитного блока из пенополистирола. После охлаждения блока в форме наступает ее разъединение.
Г. Процесс выдержки по времени блоков из пенополистирола заключается в двусторонней диффузии воздуха внутрь микропор, и выравнивание давления между внутренним объемом ячеек и атмосферой. Сушка блоков заключается в выпаривании поверхностной влаги в атмосферу.
Разрезание блоков из пенополистирола производится с помощью натянутой нагретой проволоки. Кроме того, возможно применение для разрезания блоков продольных и поперечных пил, предназначенных для работы по дереву.
2. Сырье
Сырьем для производства блоков из пенополистирола являются гранулы полистирола, содержащие порофор. В состав порофора входят низкокипящие углеводороды – изопентан, пентан и другие.
2.2 Физико-химические свойства и требования к качеству сырья
Гранулы полистирола, предназначенные для производства блоков и плит, должны иметь вид круглых шариков белого или полупрозрачного цвета. Допускается наличие серповидных и рисообразных гранул полистирола.
Требования к гранулам
Требования | Значение |
Удельная плотность собственно гранул, г/см3 | 1.03-1.05 |
Удельная плотность гранул надіп’ю, г/см3 | Около 0,6 |
Содержание мономера стирола, %, не более | 1,2 |
Вязкость 1% раствора бензина в кПа | 1,0-1,3 |
Максимальное содержание влаги, % | 5,0 |
Просев – максимальный остаток на сите с квадратным сечением | 4,0 |
2.
2.3.1. Требования к доставке сырья
Сырье доставляется в виде упаковок в закрытых средствах доставки – железнодорожным или
автомобильным транспортом. Разгрузка производится на разгрузочной рампе и сырьё доставляется на закрытый склад. Контроль за количественными характеристиками доставленного сырья производится лабораторным отделом.
Контроль должен производиться следующим образом:
а) Контроль содержания влажности в гранулах
б) Определение содержания мономера в гранулах
в) Определение вязкости гранул в 1% бензиновом растворе
г) Пробное вспенивание гранул
д) Определение удельного веса вспененных гранул
е) Анализ остатка на сите
Могут быть выполнены дополнительные испытания качества в соответствии с методикой аттестации сырья, поданной производителем или методикой, принятой в стране.
2.3.2. Складирование сырья
Сырье храниться на складе. Температура в складском помещении не должна превышать 25-ти градусов Цельсия. Упаковки должны храниться на деревянных поддонах с высотой штабеля не более 3 м. Металлические бочки складировать в высоту не более 1-3. В складе надлежит обеспечить хорошую вентиляцию.
3. Характеристика источников энергии
3.1. Водяной пар
Процесс производства пенопласта из вспенивающегося полистирола требует доставки тепла как
средства энергии нагрева для первичного процесса вспенивания, процесса формирования блоков, а также нагревания воздуха сушилки и пневматического транспортирования вспененного сырья. После проведения эксперимента с другими формами энергии, мы пришли к выводу, что наиболее практичный источник энергии – это водяной пар.
Водяной пар, применяемый для преобразования пенополистирола, должен быть насыщенным паром при давлении как минимум 0,25 мПа, не перенасыщенным водой. Оптимальное давление для формирования блоков и последующего вспенивания составляет 0,02-0,07 мПа.
формирования около 20 секунд). Параметры пара определяются при помощи термометра и манометра, установленных на линии подачи и вывода водяного пара. В целях выравнивания давления и равномерного высвобождения пара может быть установлен аккумулирующий сборник.
3.2. Электроэнергия
Электроэнергия применяется для приведения в действие вспенивателя, форм, оснащения для
разрезания блоков, пневмотранспорта и установленного освещения.
Электроэнергия поставляется от промышленных источников питания при напряжении 380 или 220 В переменного тока. Контроль и изоляция токонесущих частей производится в соответствии с требованиями службы электробезопасности предприятия.
3.3. Сжатый воздух
Сжатый воздух предназначен для приведения в действие пневматических устройств: закрывания и
открывания форм, а также выталкивания сформированных блоков. Давление сжатого воздуха от источника должно составлять не менее 5 атмосфер. Полученный сжатый воздух проходит через нагревательный элемент и распределяется при помощи системы трубопроводов. Контроль и обслуживание частей системы подачи сжатого воздуха производит служба энергобезопасности предприятия.
4. Характеристика полуфабриката
Полуфабрикатом для производства блоков из вспенивающегося полистирола являются вспененные гранулы. Они получаются на этапе вспенивания и после высушивания подаются для формирования блоков.
4.1. Физико-химические свойства
Требования | Значение | Место проведения контроля |
Удельный вес насыпью в гр./1 | 15-20 | Обслуживающая лаборатория |
Максимальный диаметр гранул в мм | 20 |
|
Минимальный диаметр гранул в мм | 0,7 |
|
Максимальное время выдержки по времени от момента вспенивания | 5 | Персонал, обслуживающий бункеры накопления |
Максимальное время выдержки по времени от момента вспенивания | 8 | Персонал, обслуживающий бункеры накопления |
Наличие агломератов размером более 4 см (вспененных | не допускается | Персонал, обслуживающий вспениватели |
Максимальное количество выкрошившихся отходов в % | 5 | Персонал, обслуживающий бункеры накопления |
4. 2. Доставка и складирование
Вспененные гранулы подаются при помощи пневмотранспорта в бункеры накопления, в которых
происходит их выдержка по времени. Температура при выдержке гранул составляет 25-30°С. Время выдержки гранул составляет от 8 часов до 5 суток. Выдержанные гранулы вместе с крошкой отходов пневмотранспортом поступают в дозаторы, находящиеся над формами.
5. Характеристика продукта
Готовым продуктом являются блоки из пенополистирола. Далее их режут на плиты по размерам,
зависящим от требований заказчика, что является уже только преобразованием готового изделия, не изменяющим его свойства.
5.1. Физико-химические свойства блоков из пенополистирола
Требования | Значения |
Удельный вес, кг/м3 | 15-20 |
Сопротивление сжатию, при деформации пробки на 10%, более кг/ | 0,4 |
Термостойкость, более, °С | 60 |
Сопротивление пропусканию тепла, в ккал/м °С в час | 0,035 |
Отсутствие разбухания в воде в течение 24 часов, менее, в % | 1,5 |
Гигроскопичность в течение 120 часов, менее, в % | 0,6 |
Размеры | Соответствуют требованиям заказчика |
6. Отходы
Максимальное количество отходов, образующихся в цикле производства изделий вспенивающегося полистирола, составляет не более 6,5%. Отходы складываются из выбракованных блоков, получающихся во время формирования и крошки, образующейся при разрезании блоков на плиты.
Отходы размельчаются в дробилке (мельнице) и в качестве крошки отходов возвращаются в
производство. Крошка в смеси с выдержанными гранулами применяется для повторного производства блоков. Максимальное количество крошки при производстве и формировании блоков не должно превышать 5%.
7. Описание технологического процесса
7.1. Общее описание процесса
7.1.1. Процесс вспенивания гранул
Первой технологической операцией по производству изделий из вспенивающегося полистирола является вспенивание гранул. Процесс вспенивания происходит благодаря расширению пор гранул. Во время вспенивания, производимого во вспенивателе насыщенным водяным паром при температуре 90-100°С, в структуре полистирола образуются микропоры. Водяной пар, подающийся во вспениватель, играет двойную роль – нагревателя и дополнительной причины вспенивания (благодаря быстрой диффузии через стенки микропор), и приводит к многократному увеличению (до 50 раз) объема гранул. Во время вспенивания гранулы размешиваются с помощью механического размешивателя с целью избегания их слипания. Водяной пар подается по системе трубопроводов, подключенной к задней части вспенивателя. Во вспенивателе гранулы размешиваются вертикальным размешивателем, состоящим из системы лопастей, предотвращающих слипание гранул. Расширенные гранулы перемещаются к горловине вспенивателя и высыпаются через засыпное отверстие, размещенное в верхней части стенки вспенивателя.
Из вспенивателя гранулы полистирола выпадают в сушилку. Поток теплого воздуха высушивает их и выдувает к горловине инжектора системы пневмотранспорта, которая доставляет гранулы в бункер.
Сушилка и система пневмотранспорта обеспечиваются теплым воздухом (более 50°С) путем нагнетания вентиляторами и нагрева паром.
В целях обеспечения возможности регулирования количества поданных гранул, предусмотрена
регулировка количества оборотов червячного дозатора, давления подводимого водяного пара.
Определение количества подаваемых гранул возложено на персонал, обслуживающий вспениватели, которые наблюдают за внешним видом гранул. Контрольно-измерительное оснащение вспенивателя состоит из регулирующих вентилей и контрольного манометра измерения давления водяного пара на линии подачи пара во вспениватель, а также весов для определения веса насыпанных вспененных гранул.
Остановка вспенивателя Каждый раз при остановке вспенивателя необходимо выполнить следующие операции:
- Остановка червячного дозатора.
- Отключение подачи пара.
- Отключение механического размешивателя по остывании.
- Опорожнение вспенивателя от вспененных гранул.
Аварийная остановка вспенивателя (отключение электроэнергии, остановка размешивателя) Требует отключения подачи пара и включение сжатого воздуха для остужения гранул. Несоблюдение этих правил приводит к дальнейшему вспениванию гранул и выходу из строя привода вспенивателя.
Возобновление работы при аварийной остановке может наступить после ее опорожнения от находящихся внутри гранул и осмотра вспенивателя.
7.1.2. Выдержка гранул по времени
Опорожняющая часть пневматического транспорта направляет гранулы в бункеры. В бункерах происходит процесс выдержки по времени вспененных гранул. Это простая технологическая операция, имеющая, однако, большое значение для дальнейшего производства и влияющая на качество сформованных изделий. Во время выдержки по времени вспененных гранул в бункерах со свободно поступающим воздухом происходит процесс диффузии воздуха внутрь гранул и выравнивания разницы давления между внутренностью гранул и атмосферой. Длительность процесса в зависимости от количества насыпанных гранул, их размера, температуры воздуха колеблется от нескольких до нескольких десятков часов. Общепризнанным является оптимальное время выдержки в течение 8 часов при комнатной температуре. Время выдержки гранул не следует продлевать более недели вследствие потери пор и ухудшения качества изготовленных изделий из передержанных гранул.
В целях уверенности, что температура выдерживания гранул, которая должна соответствовать 22-28°С, в помещении, в котором находятся бункеры, устанавливается нагревательная аппаратура, а для контроля служит настенный термометр. В целях обеспечения выдерживания по времени следует производить записи в соответствующих журналах и опорожнение выполнять в соответствии с табличками на бункерах. Выборка гранул производится из нижней части бункеров в систему пневматического трубопровода по трубам и с помощью потока воздуха транспортируется в соответствующие приспособления над формами.
Заполнение приспособлений производится периодически, каждый раз после опорожнения. Из приспособлений вспененные гранулы поступают в формы.
7.1.3. Формирование блоков из вспенивающегося полистирола
Формирование блоков из пенополистирола является наиболее важной операцией в цикле производства изделий из пенопласта. Во время этой операции засыпанные в формы вспененные гранулы дополнительно обрабатываются и слипаются между собой, образуя изделие в соответствие с заданной формой, в которой они находятся.
Смыслом этой операции является нагревание гранул, которое приводит к эффекту дальнейшего
увеличения их объема. Увеличение объема в замкнутом пространстве формы совместно с повышенной температурой материала приводит к слипанию гранул между собой и заполнению всего объема формы.
Применяемый метод производства требует использования насыщенного водяного пара как источника энергии. Водяной пар в процессе формирования, так как и при операции вспенивания, также играет роль образователя пор.
Существенным элементом цикла является его начальная фаза — это устранение воздуха, имеющегося в свободном пространстве между гранулами и стенками формы. Это производится выдуванием его струей водяного пара.
Но и дополнительная роль водяного пара в процессе формирования чрезвычайно важна. Наличие воздуха снижает скорость нагрева гранул и приводит к ухудшению качества их слипания (так называемое рассыпании блоков) или приводит к образованию в форме свободных пустот, не заполненных гранулами, так называемых каверн. Конечной операцией цикла формирования является охлаждение сформированных блоков. От этой, как кажется, простой операции очень сильно зависит качество блоков, а также удачность цикла
формования.
Цикл формования блока состоит из следующих операций:
А. Нагревание формы. Перед наполнением формы гранулами надлежит ее нагреть до температуры 80-90°С (при более высоких температурах гранулы будут слипаться сами по себе по мере их засыпания до подачи водяного пара). Во время нагревания форма должна быть закрыта, а конденсат и избыток поступающего пара должен быть направлен выделенным трубопроводом из здания. Нагревание формы имеет конечной целью избежание увлажнения гранул конденсатом, остающимся на холодной поверхности стенок формы. Поступающий на последующих этапах формирования пар должен только дополнительно нагревать стенки формы.
Б. Смазывание поверхности формы. Производится с помощью впрыскивания на внутреннюю поверхность формы раствора мыла или другого средства с целью обеспечения свободного отлипания сформированного блока от формы. Операции можно избежать, если гладкие внутренние стенки форм позволяют лёгкую выемку сформированного блока.
В. Наполнение формы. Подготовленная в соответствии с пунктами А и Б форма заполняется гранулами через сборник под давлением. Наполнение формы должно быть полным для обеспечения соответствующего качества изделия.
Г. Продувание формы водяным паром. После заполнения формы и ее закрывания с помощью пневматического привода и герметичным замыканием – контрольная лампочка на пульте управления, водяной пар подается в верхние и боковые части стенок формы и выводится (вначале как смесь воздуха и водяного пара) через камеру в нижней части формы в коллектор конденсата и водяного пара при открыто находящемся там вентиле. Давление пара в камерах во время операции должно составлять 0,03-0,05 мПа, время продувки 10-20 сек.
Применение более длительного срока продувки нежелательно, так как приводит к ухудшению слипания гранул между собой во внешней и нижней частях формы, а наоборот, сокращение времени продувки приводит к остатку воздуха в форме и образованию пустот.
Д. Собственно формирование. После проведения продувки, закрывается вентиль отвода пара и
конденсата, а также проводятся дальнейшие операции по формованию. В это время возрастает давление пара в форме до 0,04-0,06 мПа, в том числе и в свободном пространстве между гранулами. Возрастание давления должно достигнуть максимального значения и контролироваться с помощью манометров.
Во время формования гранулы разогреваются, дополнительно вспениваются и вспененные полностью занимают объем формы. Находящийся там пар проникает через стенки гранул и приводит к слипанию гранул между собой. Время формования блоков составляет 8-12 секунд.
Е. Выемка сформованных блоков. Сформированные блоки выталкиваются из формы при помощи установленного выталкивателя. Для исправного выполнения этой операции необходимо устранение причин прилипания гранул к стенкам формы, которое достигается путем нанесения средств против прилипания перед загрузкой форм. По мере эксплуатации наступает пассивность по отношению к прилипанию стенок форм и в дальнейшем можно избегать смазки.
Контрольно-измерительная аппаратура форм размещена на пульте управления. Кроме того, на линии подачи пара имеется регулирующий вентиль и манометр, а также вентиль на коллекторе конденсатора и отвода из формы. Во время приостановки работы следует прекратить подачу пара, а также сжатого воздуха и электроэнергии. Время пребывания сформованного блока в форме зависит от сырья и составляет 10-30 минут.
7.1.4. Выдержка блоков по времени
Конечно, технологической операцией является выдержка сформованных блоков по времени, когда наступает проникновение воздуха в блоки, а также его сушение. Выдержку и сушение блоков следует производить при температуре 22-30°С в течение 8 часов.
7.1.5. Разрезание блоков на плиты
Последним действием, которое производится над блоками, является процесс их преобразования в плиты. Он заключается в разрезании блоков при помощи разделительного провода.
Разрезанию следует подвергать блоки, выдержанные по времени и высушенные. Разрезание блоков разогретым проводом возможно благодаря тому, что температура разогрева провода выше температуры плавления пенопласта и оставляет за собой литую поверхность, благодаря чему усиливается значение упругости материала.
Разрезание блоков на плиты производится на оснащении, состоящем из подвижного стола и стальной рамы с натянутыми проводами.
Благодаря легкой системе регулировки расстояния между проводами можно регулировать толщину разрезанных плит в соответствии с требованиями заказчика. Разрезанные плиты из пенопласта измеряют в соответствии с требованиями, принятыми на производстве, упаковываются или доставляются навалом через склад заказчику.
8. Стоки и отходы
8.1. Технологические стоки
Стоки предназначены для стока пара, воды и конденсата из вспенивателей, форм и с места
расположения производственных мощностей. Единственная защита стока – это защита от механического занесения гранул.
8.2. Отходы
Отходы, образующиеся в процессе производства блоков, а также механического разрезания блоков на плиты вместе с гранулами, рассыпанными во время транспортировки пневмотранспортом, возвращаются в процесс производства. Количество отходов, образующихся на различных этапах производства не должно превышать 6,5% и это значение составляет разницу между нетто произведенным и брутто примененным. 8.3. Испаряемые газы
Образующиеся в процессе производства газы составляют пар и пентан. Наибольшее количество пентана находится в отводах из впенивателей. Выхлоп убирается вытяжной вентиляцией в атмосферу, где он становится безопасным. На рабочих местах, где установлены вспениватели и имеется максимальная концентрация выхлопа, установленное оборудование должно обеспечивать достаточный отвод газов.
Вытяжное вентиляционное оборудование обеспечивает многократную замену воздуха в помещении и не допускает концентрацию пентана, угрожающую пожаром или взрывом.
9. Безопасность и гигиена труда
На всех стадиях производства пенополистирол не является токсичным и нет необходимости применять средства для вредного производства.
В производственных помещениях, в которых имеется повышенная влажность (помещения вспенивателей и форм), пол следует выложить деревянным паркетом. Каждое место следует обеспечить общей инструкцией обслуживания, в которой определяется способ работы и соответствующие предписания, утвержденные службой безопасности труда, работы в соответствии с технологической инструкцией работы на данном оборудовании. Персонал к работе может быть допущен только после ознакомления с правилами технологии, эксплуатации, обслуживания и безопасности труда на данном оборудовании.
Во время эксплуатации следует обратить внимание на следующие вопросы:
А. Оснащение рабочих мест общей инструкцией по обслуживанию
Б. Подключить систему сигнализации и защиты от возрастания давления пара
В. Проводить обслуживание системы трубопроводов пара и воздуха под давлением
Г. Во время подачи пара в формы находиться за пультом управления за защитным экраном
Д. Проверять состояние пневмотранспорта
Е. Запретить курение в производственных и складских помещениях
Ж. Проверять состояние вытяжного оборудования
З. Не блокировать путей транспортирования и двери
Во всех помещениях следует поместить надписи о запрещении курения, гашения пожара водой
оборудования под напряжением, оборудовать помещения средствами пожаротушения.
Во время ремонтных работ в качестве местного освещения применять лампы с напряжением 24В.
10. Обеспечение пожарной безопасности
Объект производства относится к третьей категории объектов по пожарной безопасности. Здание
относится к классу «С», причем помещение склада сырья должно быть класса «А» и иметь огнеупорные двери.
Все помещения должны быть оборудованы гидрантами. Кроме того, все помещения должны быть
обеспечены средствами пожарного тушения в количестве не менее: углекислотные огнетушители (по два в каждом помещении), 2 углекислотных агрегата тушения (в помещении бункеров и выдержки блоков), 2 асбестовых тента (по 2 в каждом помещении).
11. Процесс двойного вспенивания гранул из пенополистирола.
Процесс двойного вспенивания гранул применяется для уменьшения расхода сырья, менее 14-15 кг/м3.
Процесс заключается в том, что во время первого вспенивания, удельная плотность гранул насыпью находится в пределах 16-18 кг/м3, а после их высушивания проводится повторное вспенивание и удельный вес насыпью составляет 11-12 кг/м3.
Гранулы после проведения процесса выдержки предназначаются для формирования изделий с плотностью 12-15 кг/м3. Процесс вспенивания можно проводить многократно и довести плотность до 5-7 кг/м3, однако формование изделий из таких интенсивно вспененных гранул затруднено, так как в них остается небольшое содержание порофора. Также изделия из него характеризуются невысокой стойкостью к механическим воздействиям, когда содержание полимера составляет 0,5-0,7 % от объема, а воздуха соответственно 99,3-99,5% объема.
Процесс многократного вспенивания был запатентован еще в 1961 году.
11.1. Теоретическое обоснование процесса двукратного вспенивания.
Из кинетической кривой вспенивания следует, что процесс проходит интенсивно в течение первых 2-3 минут и масса насыпанных гранул уменьшается с 550 до 25-30 кг/м3 или в 18-22 раза, соответственно увеличивается объем, а при более долгом вспенивании процесс затормаживается, даже может иметь место увеличение плотности гранул. Это связано с потерей порофора при вспенивании. Во время нагревания гранул до температуры вспенивания (около 100°С) находящийся в них порофор-пентан (химическая формула С5Н12, температура кипения – 36,5°С) превращается в пар. Его утечка невелика и для поддержания равновесия давления гранулы расширяются. Основные потери происходят по причине увеличения объема, а главное времени вспенивания. В процессе многократного вспенивания гранул порофор разрежается воздухом, проникающим в гранулы в процессе выдержки.
Время двойного вспенивания почти совпадает со временем одинарного вспенивания, поэтому потери порофора одинаковы в обоих случаях. Во всех случаях вспенивания существенна роль пара. Он является дополнительным источником
вспенивания. Благодаря сильной диффузии он проникает в образующиеся микропоры и приводит в соответствие давление в гранулах с внешним давлением.
11.2. Процесс двойного вспенивания.
Технологический процесс двойного вспенивания выглядит следующим образом: на первом этапе
вспенивания, проводящейся в атмосфере водяного пара, надлежит довести удельный вес гранул до 16-18 кг/м3. Условиями получения такой интенсивности вспенивания являются соответствующий подбор скорости их дозирования, времени пребывания во вспенивателе или температуры вспенивания посредством использования смеси пара и воздуха.
После первой стадии гранулы высушивают на месте в подвешенном состоянии при как можно более высокой температуре и выдерживают на месте. Расчеты по выдерживанию для 1 ступени: температура 15-25°С, время 3-8 часов. Высушенные гранулы повторно поступают во вспениватель и при помощи пара или смеси его с воздухом вспениваются до достижения удельного веса 11-12 кг/м3. Двукратно вспененные гранулы высушивают подобно 1 ступени и направляют в бункеры, в которых их выдерживают. Расчеты по выдерживанию для 2 ступени: температура 15-25°С, время 5-15 часов. После выдержки гранулы предназначаются для формирования блоков. Условия формирования блоков следует подбирать опытным путем, имея в виду повышенную деформируемость гранул при низком удельном весе на сжатие у сформированных блоков.
11.3. Технология процесса и оснащение
Первое вспенивание Во время этого этапа гранулы должны достичь удельного веса насыпью в пределах 16-18 кг/м3. Для этих целей необходимо подобрать определенные параметры вспенивания. Этого можно достичь посредством:
- уменьшения уровня засыпания во вспениватель, что приводит, однако, к уменьшению
производительности - уменьшение количества подаваемого пара во вспениватель и тем самым уменьшение температуры во вспенивателе
- применение смеси пара и воздуха
- сокращение времени пребывания гранул во вспенивателе посредством увеличения скорости
дозирования.
Последний вариант является наиболее приемлемым, потому что не уменьшает производительность вспенивателя. Чтобы количество подаваемого через шнек сырья стало меньше (при полном заполнении шнека) при максимальных оборотах надлежит увеличить количество оборотов шнека путем замены ременной передачи.
11.4. Сушение гранул после первого вспенивания
Процесс сушки проводится в существующих сушилках. Не требуется ее специальная доработка для двойного вспенивания.
11.5. Выдержка гранул после первого вспенивания
Несмотря на то, что гранулы после первого вспенивания имеют более высокий удельный вес, время выдержки гранул сокращается и составляет 3-8 часов. Как известно, время выдержки гранул меньшего диаметра меньше. Температуры выдержки составляют 15-25°С. 11.6. Второе вспенивание Процесс второго вспенивания проводится аналогично первому. Следует подобрать те же параметры:
- скорость дозирования
- температура во вспенивателе
Основными критериями оценки правильности работы вспенивателя является определяемый удельный вес гранул насыпью, а также отсутствие появления пыли по выходу из сушилки. В случае появления пыли из гранул, надлежит уменьшить температуру вспенивания (уменьшить
количество подаваемого пара или обогатить смесь воздухом) или увеличить скорость прохождения гранул (дозирование) через вспениватель путем увеличения оборотов подающего червякового шнека.
Вспененные повторно гранулы, в связи с их малым удельным весом, более чувствительны к
механическим повреждениям во время их транспортировки. Поэтому следует уменьшить скорость
транспортировки путем изменения скорости работы вентилятора.
11.7. Выдержка гранул после второго вспенивания
Из сушилки через инжектор гранулы направляются в существующие бункеры, где происходит процесс диффузии воздуха в образовавшиеся микропоры. Оптимальное время выдержки после второй ступени вспенивания составляет несколько часов в зависимости от размера гранул. Температура выдержки должна составлять, как и во время первой выдержки, в пределах 15-25°С. Время выдержки при одинаковом удельном весе зависит от размера гранул.
11.8. Процесс формирования блоков
Процесс формирования блоков при двукратном вспенивании не сильно отличается от обычного
процесса. Также следует обеспечить продувку формы, наполненной гранулами.
Давление пара во время этой операции должно быть в пределах 0,1-0,2 атмосфер, а время продувки как можно меньшим, в границах нескольких секунд. Расчеты продувки и дальнейшая подача пара должны обеспечивать равномерное нагревание гранул во всем рабочем объеме формы.
Давление пара во время формования должно составлять 0,4-0,7 атмосфер в зависимости от качества гранул (удельного веса содержащегося полимера). Время формирования с учетом повышенной чувствительности к механическому воздействию не должно быть большим, потому что это приведет к осыпанию (появлению пыли) блоков, даже во время формирования и далее в процессе охлаждения.
Общее время воздействия пара должно составлять 15-40 секунд, время охлаждения 5-10 минут, в
зависимости от температуры формования, а также давления пара, конструкции формы и ее герметичности. Данные должны определяться опытным путем с учетом качества сырья, а также удельного веса после второго вспенивания.
12. Описание и порядок эксплуатации вспенивателя, предназначенного для
ступенчатого вспенивания пенополистирола
12.1. Описание и порядок эксплуатации
Вспениватель следует устанавливать на твердой ровной поверхности и выравнивать по длине и ширине при помощи уровня. Первой технологической операцией является вспенивание гранул. Процесс вспенивания возможен благодаря порофору, который содержится в гранулах. Во время вспенивания, производимого при помощи водяного пара, подаваемого во вспениватель при температуре 90-100°С (давление пара 0,1 мПа) в монолите полистирола возникает микропористая структура. Водяной пар, подаваемый во вспениватель, играет двойную роль: основную – нагревание и дополнительную – источника вспенивания (благодаря высокой скорости диффузии через стенки микропор), приводит к многократному (до 50 раз) увеличению объема гранул. Во время вспенивания гранулы перемешиваются при помощи механической мешалки с целью предотвращения их слипания.
Водяной пар подается во вспениватель при помощи трубопровода к нижней его части. Во вспенивателе гранулы перемешиваются вертикальной мешалкой, состоящей из системы лопастей, предотвращающей слипание гранул. Увеличивающиеся в объеме гранулы перемещаются в верхнюю часть вспенивателя и опускаются через отверстие засыпания, размещенное в верхней части стенки вспенивателя.
Из вспенивателя гранулы полистирола выпадают в сушилку. Поток теплого воздуха высушивает их и выдувает в горловину (инжектор) пневмотранспорта, который доставляет их в бункеры.
Сушилка и транспортная часть приводится в действие теплым воздухом (более 50°С) при помощи
вентиляторов и обогревается паром.
В целях возможного регулирования производительности и насыпного веса гранул, вспениватель
имеет:
А. Возможность двукратного вспенивания,
Б. Регулировку скорости оборотов шнековых дозаторов.
Определение насыпного веса является обязанность обслуживающего персонала, который проводит внешний осмотр вспененных гранул. Контрольно-измерительное оборудование состоит из вентилей закрывания и манометра контрольного давления водяного пара на линии до вспенивателя, а также винта, регулирующего обороты червячной передачи.
12.2. Требования по безопасности труда
- вспениватель может обслуживаться только персоналом, ознакомленным с принципом его действия и устройством, а также с правилами безопасности труда
- обслуживающий персонал должен соблюдать общие правила безопасности труда, обязательные на предприятии
- рабочее место должно быть надлежащим образом освещено и быть чистым, а работник, обслуживающий вспениватель, должен работать в одежде и обуви, находящейся в надлежащем состоянии
- при манипуляциях с паровым вентилем руки должны быть одеты в рабочие рукавицы
Запрещается:
- открывание дверки главного сборника вспенивателя, а также выполнение внутреннего осмотра сборника во время работы мешалки
- включение двигателей привода при открытых защитных кожухах системы ременной передачи
- манипулирование рукой в контрольном лючке червячной передачи при работающем оборудовании.
12.3. Порядок работ перед началом работы вспенивателя
Перед началом работы вспенивателя необходимо выполнить следующие действия:
- Проверить герметичность системы подачи пара по трубопроводу при давлении 0,1 МПа.
- Убедится в правильности подключения к электросети.
- Проверить состояние защитного кожуха на ременной передаче.
- Мусор, попавший в главный сборник, может повредить мешалку и сетку.
- Мусор, попавший в сборник засыпания гранул, может повредить червячную передачу, подающую гранулы в главный сборник вспенивателя.
12.4. Обслуживание во время работ
- Тщательно закрыть дверки на главном сборнике вспенивателя.
- Осторожно открыть паровой вентиль и нагреть главный сборник в течение 10-15 минут.
- Наполнить главный сборник гранулами при помощи червячной передачи. Во время работы сборник (первая ступень вспенивания) должен заполняться автоматически.
3а. Для заполнения во второй ступени вспенивания наполнить бункер второй ступени вспенивания
гранулами, прошедшими через первую ступень при помощи червячной передачи большего диаметра. Бункер второй ступени заполняет себя при помощи вентилятора.
- Включить двигатель мешалки в главном сборнике.
- Включить червячную передачу, подающую гранулы в главный сборник.
- Включить пневмотранспорт, а также сушилку.
- Следить за текущей работой вспенивателя.
12.5. Обслуживание по окончании работ
- Выключить червячную передачу.
- Выключить червячную передачу по опорожнении засыпного сборника.
- Перекрыть подачу пара во вспениватель и подать сжатый воздух в целях охлаждения
сборника. - Выключить двигатель привода мешалки в главном сборнике по охлаждении (примерно через 60 минут).
- Выключить вентилятор, а также сушилку.
- Выключить подачу электроэнергии главным рубильником.
Каждая остановка вспенивателя требует:
- Остановка червячного дозатора.
- Отключение подачи пара.
- Отключение механической мешалки по охлаждении.
- Опорожнение вспенивателя от вспененных гранул через дверки во вспенивателе.
12.6. Порядок действий при аварии (выключение электроэнергии, остановка
мешалки)
Требует немедленного отключения подачи пара и включения подачи сжатого воздуха с целью
охлаждения гранул. Невыполнение этих правил может привести к слипанию гранул, находящихся внутри в агломерат, что может повредить оборудование привода вспенивателя.
Возобновление работы вспенивателя после аварийной остановки может производиться после опорожнения находящихся внутри гранул и осмотра вспенивателя
Из чего делают пенопласт
Существует такой вид материалов, которые называются вторсырьем. Это значит, что их можно использовать повторно. Одним из таких материалов является пенополистирол или пенопласт. С ним мы сталкиваемся очень часто. Например, в нем может быть упакована техника, посуда, мебель. Пенопласт отличный транспортировочный материал. К тому же это и прекрасный утеплитель. Многие люди, у которых скопились пенопластовые изделия, попросту выбрасывают их. Однако, мало кто знает, что их нельзя выбрасывать на мусор, а нужно утилизировать или переработать. Все дело в том, что он может загрязнять окружающую среду. Отходы пенопласта не разлагаются. Пусть на растения они никак не влияют, однако, животные могут пострадать. Как же тогда быть?
Пенопласт придется переработать или сдать переработчикам, которые сделают все своими руками. В этой статье мы узнаем, из чего делают пенопласт, для чего нужна переработка и как сделать пенопласт в домашних условиях.
Процесс создания пенопласта
Этот материал делается из пенополистирола, путем его вспенивания. Практически на 98% он состоит из газа. Существует 6 этапов создания пенопласта в промышленных условиях:
- Вспенивание.
- Высушивание образовавшихся гранул.
- Стабилизация.
- Выпекание.
- Созревание.
- Нарезка.
Рассмотрим каждый из этапов. Для начала сырье засыпают в пенообразователь, после чего парогенератор образует давление, при котором гранулы начинают увеличиваться от 20 в 50 раз. Весь процесс вспенивания проходит 5 минут. При достижении нужного размера сырье выгружается для сушки. Она нужна для того, чтобы лишняя влага на гранулах испарилась. Все происходит за счет горячего воздуха, направленного снизу вверх. Сушка и встряска выполняются около 5 минут.
Дальше сырье перемещается в бункеры, где на протяжении 4-12 часов вылеживаются. После этого пенопласт формируют или выпекают. Основная задача — соединить все гранулы, создав плиту или другой нужный элемент. Для этого они засыпаются в форму и поддаются давлению под высокой температурой от пара. Выпекание длится 10 минут. Дальше готовый пенопласт должен вылежаться, чтобы избавиться от влаги и напряжения внутри. Иногда созревание длится целый месяц. В конце этого этапа блок устанавливается на станок, который нарезает материал, формируя его. Станок имеет нихромовые струны, что нагреваются и с легкостью режут пенопласт.
На производстве дополнительно выполняется и переработка пенопласта. Ведь при создании остаются куски. Вот они-то и перерабатываются. А для чего вообще перерабатывать материал?
Переработка материала — зачем и как
Если говорить о большом производстве, то цель понятна — отходов много, а это дополнительные средства. А что сказать о нас, рядовых пользователях? Все дело в том, что с годами материала в доме становится все больше и больше. Он занимает место и накапливается больше. Сжигать его не рекомендуется, так как он выделяет вредные вещества, а выбросить — тоже не вариант.
Вот и получается, что правильное и эффективное решение — отдать на переработку или сделать это своими руками. Такая утилизация пенопласта поможет использовать его для другой цели и избавится от лишнего мусора дома. Чтобы сделать это своими руками, важно:
- определится с целью переработки и создания пенопласта;
- подобрать оптимальное место, где можно воплотить все в жизнь;
- определится со способом воздействия на пенопластовые отходы.
Многие останавливаются на том, чтобы использовать пенопласт в качество упаковочного материала. Хранить его в готовом виде проблематично, а вот измельчение поможет решить проблему. Чтобы заняться переработкой, нужна дробилка для пенопласта.
Существует несколько способов переработки или утилизации пенопласта:
- Используя измельчитель. Она поможет сделать дробленый пенопласт, который в дальнейшем можно использовать для разных целей. Если дроблёнка отсутствует, то все можно сделать своими руками. Но, есть одна особенность — гранулы легкие, поэтому для ручной работы потребуется мешок или другая емкость.
- Что касается утилизации, то сделать это очень просто. Если в пенопласте вы больше не нуждаетесь, достаточно обработать его концентратом из цедры цитрусовых.
А еще проще купить ацетон или растворитель и растопить его в них. При воздействии с этими жидкостями пенопласт становится жидким.
- Последний вариант — переплавка пенополистирола посредством нагрева. Готовое сырье пригодно для садового участка на даче. Его смешивают с грунтом для грядок или клумб. Благодаря этому влага будет дольше сохраняться в земле и лучше впитываться. При сильной засухе почва не потрескается. Однако такая почва не будет поддерживать гниение.
Некоторые могут спросить: а зачем мне дробленый пенопласт? Его можно использовать не только для транспортировки, но и как теплоизоляционный материал. Давайте рассмотрим, где еще он пригодится.
Использование переработанного пенополистирола
Строительство — это процесс, который требует больших вложений. И если у вас есть пенопласт, то он точно найдет свое применение на стройке. Например, крошка пенопласта может быть использована в качестве заполнителя для впадин на участке и неровностей. Понятно, что дорогу им не выровнять, но дорожку или другую неровность легко. Переработанным пенополистиролом может быть заполнена скважина, разного диаметра отверстия или полости.
Обратите внимание! За многие годы материал не будет меняться и сохранится в том виде и в форме, в которой его оставили. Он прекрасно впитывает и оттает влагу. Потому металлические емкости с пенополистиролом не так подвержены коррозии.
Что касается строительного бизнеса, то переработанный пенополистирол используется для создания облегченного кирпича. Его структура такова, что в народе он получил название дырчатый. Появился даже облегченный бетон, который, как заявляют специалисты, не менее прочен, чем обычный. Это полистиролбитон — прекрасный строительный материал. В его состав входит портландцемент, непосредственно гранулы пенопласта, вода и воздухововлекающая добавка. Иногда в смесь добавляют песок.
Еще одна сфера использования — это дизайнерское дело. Дизайнеры очень любят пенопласт и используют его в самых разных направлениях. Он используется для декорирования стен, создания горшков, кашпо или подобных аксессуаров. Очень красиво смотрятся садовые фигурки или подставки. Их создают посредством засыпки в формы и их нагревания. Можно найти самые разные варианты того, что сделать из полистирола в домашних условиях.
Переработка материала своими руками
Если вы хотите знать, как именно можно перерабатывать пенопласт, то предлагаем рассмотреть пошаговую инструкцию. Все что нужно — это достаточное количество пенопласта и дробилка. Тогда можно получить гранулы пенопласта и использовать их в своих целях. Если вы не имеете собственной дробилки для пенопласта, то ее можно сделать своими руками. Ведь заводские модели имеют очень высокую цену.
Вот что потребуется, чтобы у вас в хозяйстве появился новый полезный инструмент:
- канализационная ПВХ труба, диаметром 50 мм;
- рулетка и маркер;
- пилка по металлу;
- деревянный брус, который бы поместился внутрь трубы;
- металлические саморезы;
- шуруповерт и дрель;
- металлические шпильки с болтами;
- ДСП или фанера, для создания короба.
При помощи такого набора инструментов и материалов, можно создать рабочую дробилку для пенопласта. С ее помощью листы или другие поделки из пенопласта будут превращаться в крошку. В основе механизма — подвижная часть с зубцами, которые и дробят пенопласт на гранулы. А благодаря контейнеру или коробу материал легче направлять к вращающемуся механизму. Как именно создать дробилку вы узнаете из данного видео.
Итак, когда дробилка готова, можно приступать к работе. Вот что нужно сделать:
- Выбрать подходящее место. Как вариант выберите гараж, склад, кладовку или сарай.
- Установить дробилку, позаботившись о емкости под ней, куда и будет попадать крошка. Это может быть ведро, мешок или деревянный короб.
- Пенопластовые листы дробить просто. А вот что касается фигурных изделий, то их лучше заранее разломить на куски руками.
- Теперь остается включить наш самодельный агрегат и постепенно перерабатывать сырье.
Благодаря подобной технологии большинство гранул останутся целыми. А это значит, что они будут как никак лучше справляться со своей задачей. Только нужно быть осторожными, так как пенопласт электризуется и очень легкий. Важно позаботиться, чтобы в помещении не было сквозняков, а то потом придется убирать все с пола. Вот теперь то пенопласт можно собрать в мешки и использовать сразу же или хранить, пока он не дождется своего часа.
Обратите внимание! Если вы расплавите пенопласт при помощи ацетона, то его можно использовать в жидком виде как клей. Хотя смесь нельзя назвать безопасной.
Подведем итоги
Пенопласт — прекрасный и универсальный материал. Он может быть использован в самых различных сферах. Основное его преимущество — дешевизна, легкость, невосприимчивость к влаге и прекрасные показатели шумоподавления и звукоизоляции. А тот факт, что его можно использовать повторно, делает материал просто незаменимым в строительстве. Поэтому если у вас есть небольшое количество пенопласта, которое попросту валяется без дела, почему бы не дать ему новую жизнь? Переработав, его можно использовать как сухой утеплитель. А если хорошо подумать, то вариантов использования найдется масса.
Отправить комментарий
Технология производства пенопласта / Оборудование для производства пенополистирола (полистирола).
Технология |
---|
Плиты из пенопласта полистирольного изготавливаются беспрессовым способом из суспензионного вспенивающегося
полистирола путем формования блоков пенопласта в крупногабаритных формах (блок-формах) методом теплового удара. |
Упрощенная технологическая схема производства пенопласта: |
Гранулы поступают
в бункер предвспенивателя, где происходит первый тепловой удар, после
гранулы пневмотранспортом доставляются в бункер вылеживания, где выдерживаются
от 12 до 24 часов в зависимости от качества исходного сырья и желаемого
качества конечного продукта. Производство безотходное: весь некондиционный материал дробится и добавляется к предварительно вспененному полистирольному грануляту перед формованием его в блоки в количестве 10-15% на один блок. |
Телефон: +7 473 256-46-33, +7 920 407-62-26, e-mail: [email protected]
Завод изделий из пенопласта
История завода
16 лет успешного производства разноплановой продукции из пенопласта
2003 г.
Начало пути. 16 лет назад
На заводе появилась первая линия производства листового вспененного пенополистирола общей мощностью 6 000 м3 в год. Мы стали выпускать простые и нестандартные изделия из пенопласта.
2005 г.
13 лет назад
Благодаря закупке еще одной импортной производственной линии, за 2 года увеличили объем производства в 10 раз (до 60 000 м3). Завод запустил новые направления: производство трубной теплоизоляции и фасадного декора.
2007 — 2010 г.
11 лет назад
Расширили производственные площади за счет переезда на новую площадку, модернизировали оборудование для ускорения работы без потери качества. За счет этого объем выпускаемой продукции увеличился до 120 000 м3 в год. Завод начал производить формованные плиты и расширил складские площади, что повысило возможности отгрузки заказов прямо со склада.
2011 г.
9 лет назад
Перешли на производство полного цикла, объем выпуска продукции достиг 360 000 м3 в год. Постоянно улучшали итоговые характеристики вспененного пенополистирола, что позволило нам выпускать пенопласт любых марок на основе пожеланий наших клиентов.
2014 г.
6 лет назад
Заменили стандартную производственную линию автоматизированной. Благодаря этому мы увеличили производство фасадного декора, трубной изоляции и фигурных изделий в 2 раза. Появилась возможность упаковки готовой продукции размером до 4 метров.
2015 г.
5 лет назад
Купили патент на производство фасадных панелей Полифасад. Уникальная технология позволила выпускать плиту, которая одновременно декорирует и утепляет фасад здания.
2016 г.
4 года назад
Запустили производство упаковочного материала Лузфил с выпуском до 10 000 м3 в год. Благодаря нашим сотрудникам был заключен контракт на поставку американского сырья для производства этого материала.
2017 г.
3 года назад
Создали собственную технологию производства дренажной системы и запатентовали ее. Запустили производство дренажной системы с названием ЛАЙТРОК. Развили производственную мощность более, чем 100 000 пог.м и организовали дилерскую сеть по РФ.
2018 г.
2 года назад
Завод приобрел роботизированный манипулятор Yaskawa для обработки пенопласта и дерева при производстве фигурных изделий с точностью до 1 мм. Это позволило нам выпускать художественные 3D изделия, модели для ЛГМ и упаковку любой сложности. Также мы расширили производственное помещение на 500 м² и увеличили штат сотрудников.
2019 г.
1 год назад
Запустили услуги по нанесению теплоизоляции из пенополиуретана и гидроизоляции полимочевиной. Чтобы закрыть вопрос с утеплением нестандартных объектов и перевозки оборудования для утепления, мы добавили в автопарк завода новую транспортировочную машину.
2019 г.
1 год назад
Нацелились на безотходное производство, поэтому закупили новое оборудование для переработки отходов пенопласта и запустили производство гранул: крошки и дробленки. Запустили в городе Екатеринбург масштабную акцию по приему отходов пенопласта.
2020 г.
Всё ещё впереди
Запустили новое направление по производству изделий из стеклопластика: обучили персонал, закупили материалы и приобрели специальное оборудование. Продолжаем развивать собственную дилерскую сеть: на сегодняшний день у нас есть дилеры в Екатеринбурге, Краснодаре, Тюмени, Перми, Казани, Саратове, Новосибирске и Санкт-Петербурге.
Изготовление изделий из пенопласта под заказ в Москве
Морозная свежесть, запах первых мандаринов… Вы уже чувствуете настроение праздника?
Мы все с нетерпением ждали этого момента, а потому в преддверии праздника коллектив компании “ТОП-Пенопласт” от всего сердца желает Вам праздничного настроения, любви, здоровья и исполнения всех желаний!
Пусть вас окружают самые красивые вещи, лучшие люди и только положительные эмоции!
С Новым 2021 годом!
Буквы из пенопласта
Объемные буквы из пенопласта – новинка современного рынка, которая помогает быстро и эффективно привлечь внимание потенциальных клиентов к своей компании!Вывески
Качественная, грамотно подготовленная реклама – обязательная составляющая успеха любой компании.
Фигуры
Фигуры из пенопласта — максимум преимуществ от компании «ТОП-Пенопласт»! Современные и недорогие решения для декорирования любых пространств.Садово-парковые скульптуры
Наибольшую популярность в наши дни приобрели садово-парковые скульптуры из пенопласта, которые выступают прекрасной альтернативой каменному, деревянному и металлическому декору.Муляжи
Муляжи из пенопласта – выгодный и доступный рекламный продукт! Очень часто при оформлении торговых и выставочных залов, проведении рекламных компаний или театральных постановок.Фасадный декор
Фасадный декор из пенопласта – роскошные решения для внешнего оформления Вашего дома! Они создают особый образ дома, придавая ему индивидуальность и помогая выразиться его владельцу.Резка пенопласта
Фигурная резка пенопласта – современное оборудование для максимальной точности, которое позволяет создавать фигуры любой сложности.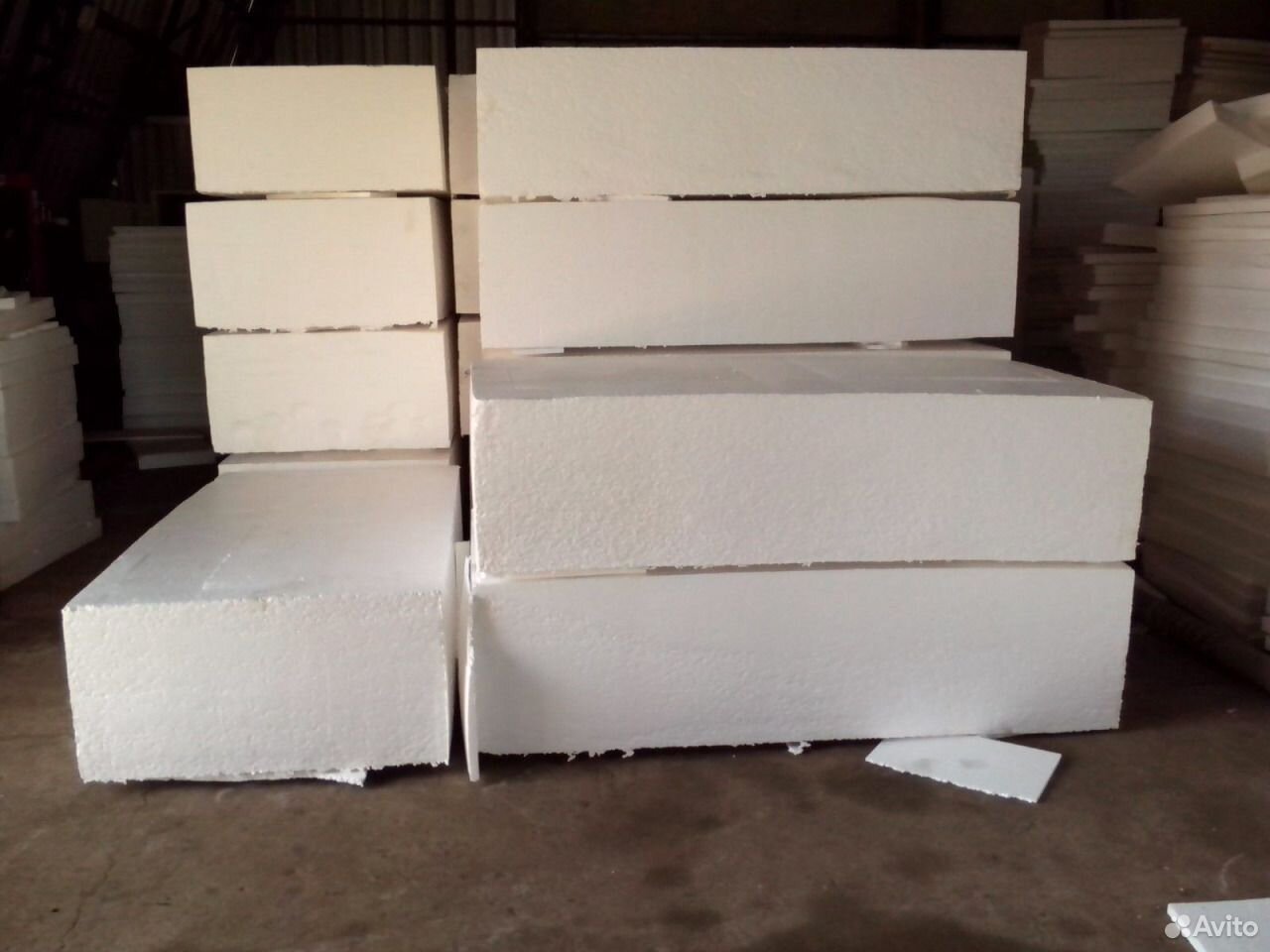
Шары из пенопласта
Шары из пенопласта – создайте гармонию в своем доме! Они с легкостью заменят елочные игрушки, внесут гармонию в любой интерьер и просто создадут праздничное настроение.Светящиеся вывески
Светящиеся объемные буквы видны со многих ракурсов и в то же время неоновые трубки хорошо защищены от воздействий как атмосферы, так и вандалов.
Упаковка
Упаковка из пенопласта – надежная защита для самых хрупких предметов! У нас Вы можете приобрести продукцию, которая обеспечить высокую степень защиты бытовой техники, мебели, стеклянных изделий.Макеты
Макеты из пенопласта – мы создадим для Вас настоящие шедевры! Обращайтесь в «Топ-пенопласт», здесь Вас ждут настоящие профессионалы, для которых нет ничего невозможного!Реклама из пенопласта
Качественная, грамотно подготовленная реклама – обязательная составляющая успеха любой компании. Она привлекает к себе внимание потенциальных клиентов.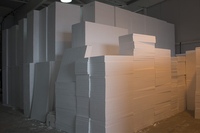
Буквы для свадьбы
Практически ни одна свадьба не обходится без яркой фотосессии. Красивые кадры обеспечат долгую память об этом событии, а объемные буквы из пенопласта придадут фотографиям дополнительную изюминку.Изготовление пенопластовых МАКЕТОВ И МОДЕЛЕЙ точно в срок и по лучшим ценам в Москве!
Товары из пенопласта являются прекрасным украшением интерьера или фасада дома, оригинальной деталью любой рекламной компании, неотъемлемым атрибутом свадебной или новогодней вечеринки, изысканным элементом фотосессии! Данный список можно продолжать бесконечно.
Если Вы хотите купить предметы из пенопласта от производителя по лучшим в Москве ценам, обращайтесь в компанию «ТОП-Пенопласт».
ПРИМЕНЕНИЕ ТОВАРОВ ИЗ ПЕНОПОЛИСТИРОЛА И ИХ ОСНОВНЫЕ ПРЕИМУЩЕСТВА
В последнее время пенопластовые атрибуты используются практически повсеместно: в упаковочной и пищевой индустрии, в строительной отрасли, в бытовой сфере, для утепления стен, полов и потолков, во флористике, в дизайне интерьеров, в организации праздничных мероприятий и проведении рекламных компаний. Элементы из экструдированного пенополистирола зачастую применяются при отделке фасадов зданий, дверных и оконных проемов, потолков, а пенопластовые фигуры нередко можно увидеть в парках, скверах и на заднем дворе многих загородных домов.
Пенопласт прочно занял свое место в архитектурно-декоративном оформлении, вытесняя традиционные материалы, такие как камень, мрамор или гипс.
В первую очередь, это связано с его преимуществами:
- при изготовлении изделий из пенопласта им можно придать любую форму, так как данный материал очень легко обрабатывается;
- возможность производства деталей из пенополистирола с идеально ровной поверхностью без каких-либо швов;
- малый вес материала;
- легкость и удобство монтажа, без применения специальных средств;
- стойкость пенопластовых элементов к внешним воздействиям – ветру, дождю, воздействию ультрафиолета и перепадам температур;
- экологичность — производство изделий из пенополистирола абсолютно безопасно и нетоксично;
- долговечность – благодаря специальным покрытиям пенопласт не подвержен образованию грибка или плесени, гниению и поражению насекомыми;
- пожаробезопасность – в случае возгорания пенопласт быстро самозатухает;
- доступная стоимость изделий из пенопласта, так как это самый недорогой материал, используемый к примеру для архитектурного оформления.
ОСОБЕННОСТИ ИЗГОТОВЛЕНИЯ ТОВАРОВ ИЗ ПЕНОПОЛИСТИРОЛА
Компания «ТОП-Пенопласт» занимается производством изделиЙ из пенопласта практически любого размера и сложности. Вы всегда можете заказать у нас буквы из пенопласта, слова и надписи, пенопластовые фигуры и фигурки, элементы фасадного декора и многое другое. Кроме того, мы рады предложить Вам производство макетов на заказ по Вашему индивидуальному эскизу.
Наши специалисты могут предложить Вам изготовление элементов декора из экструдированного (пенопласта повышенной плотности) и обычного пенопласта по весьма привлекательным в Москве ценам.
Производство изделий из пенопласта осуществляется на современных станках с ЧПУ, методом фигурной и контурной резки, позволяющих изготовлять любые детали с максимальной точностью.
После этого все атрибуты тщательно зашкуриваются, грунтуются и покрываются краской, а в случае необходимости и специальными составами, защищающими их от неблагоприятного внешнего воздействия.
В ряде случаев для придания пенопластовым моделям большей устойчивости, детали могут закрепляться на металлический каркас.
Для всех клиентов, заказавших у нас поделки из пенопласта, мы можем оказать услуги по их доставке, а в случае необходимости монтажу в пределах Москвы и Московской области. Доставка готовых изделий возможна также и в другие регионы РФ.
Мы все еще не убедили Вас в том, что пенопласт – это модно, современно и надежно? Знакомьтесь с нашими работами, эстетичность и разнообразие которых станет для Вас приятным сюрпризом!
НАШИ КЛИЕНТЫ
Состав, свойства и применение пенополистирола
Пенополистирол широко применяется в строительстве в качестве универсального утеплителя. Представляет собой газонаполненный материал, получаемый из полистирола и его производных, а также из сополимеров стирола. Благодаря своей структуре пенополистирол чрезвычайно лёгкий и недорогой материал, обладающий уникальными теплоизоляционными свойствами.
Состав пенополистирола
Содержание статьи
При вакуумном способе получения, газа в продукте вообще не будет. Вместо первого компонента, в зависимости от необходимости, могут использоваться другие полимеры. Например:
- Полимонохлорстирол;
- Полидихлорстирол;
- Сополимеры стирола с прочими одномерными (например, акрилонитритом).
Технология получения материала
Технология получения пенополистиролаТребует наличия на стадии изготовления разнообразных вспенивающих веществ для заполнения массы полимерного вещества газами. Это могут быть лёгкие для кипения углеводороды (такие, как петролейный эфир, изопентан, пентан или обычный дихлометан) или специальные вещества, которые образуют газ (аммоний нитрат, диаминобензол, азобисизобутиронитрил).
Помимо всего перечисленного, дополнительными компонентами получаемого изделия могут становиться разнообразные вещества, которые так или иначе улучшают его характеристики:
- Антипирены — объект статьи сам по себе не обладает высокой жароустойчивостью, а это значит, что в отдельных случаях эту жароустойчивость необходимо повышать при помощи добавления в полистирол веществ, которые обеспечивают достаточную огнезащиту;
- Пластификаторы — для уменьшения ползучести смеси в процессе застывания и высыхания;
- Наполнители — для изменения характеристик материала в целом и заполнения гранул чем-то ещё;
- Красящие вещества — для придания готовому пенополистиролу определённых эстетических качеств.
Исходя из названия этого материала, можно сделать вывод о том, что этот объект получают из исходного сырья — полистирола. В обычном случае, расплавленную массу полимера наполняют газом при помощи вспенивания.
В дальнейшем, готовая смесь полимерного материала и газа нагревается паром. Благодаря этому, гранулы увеличиваются в объёме и распределяются равномерно по всему объёму смеси и спекаются друг с другом в одно целое. В результате полистирол резко набирает в объёме.
Схема цеха по производству пенополистиролаДля получения огромных объёмов необходимого материала, количество полимера относительно небольшое. Сам материал очень лёгкий и после формования готов к дальнейшей физической обработке и использованию.
Помимо описанного способа, существуют методы получения этого материала при помощи углекислого газа (в том случае, если необходим жаростойкий пенополистирол), или без какого либо газа вообще (гранулы в нём заполнены вакуумом).
Свойства
Изделие обладает рядом физических химических и биологических свойств. Если говорить о механических особенностях, то можно судить о значительной прочности на воздействие краткосрочных нагрузок и нагрузок средней длительности. Такой объект в международных классификациях характеризуется как жесткий пенопласт (ДИН 7726). В соответствии с таблицами, этот материал может выдержать десятипроцентное сжатие в объёме. Но, в нормативных документах отмечается, что после такого сжатия, изделие уже не восстановит свою первоначальную форму.
Отдельными физическими свойствами, являются теплоизолирующие свойства пенополистирола, его водонепроницаемость (однако, не стоит забывать про диффузию водяного пара) и регулируемую (в зависимости от условий и качества изготовления) пластичность.
Утепление пола пенополистироломВ сравнении с другими материалами в определённых документах приводятся значения необходимой толщины покрытия из других материалов, что бы соответствовать толщине изоляции из пенополистирола всего в 12 сантиметров. При одном взгляде на эти цифры, всё становится понятно.
По действующим российским строительным нормам толщина стен, одинаково препятствующих теплопотерям в здании, должна быть примерно:
- Железобетон — 4 м 20 см;
- Кирпич — 2 м 10 см;
- Керамзитобетон — 90 см;
- Дерево — 45 см;
- Минеральная вата — 18 см;
- Пенополистирол — 12 см.
Эти показатели весьма впечатляют. На сегодняшний день, есть совсем немного причин для того, чтобы отказываться от теплоизоляции из субъекта статьи.
Характеристики
Стоит остановиться подробнее на каждой из характеристик пенополистирола.
Схема утепления фундаментаКрайне низкая теплопроводность
Благодаря тому, что воздух составляет подавляющий объём во всём готовом изделии, можно судить о хороших теплоизолирующих качествах пенополистирола(а значит такой материал будет замечательно сохранять тепло в помещениях, повысит эксплуатационные сроки трубопроводов, обеспечит высокую надёжность и понизит потери тепла на тепломагистралях, послужит хорошей изоляцией на стационарных холодильных установках, защитит товары на складских помещениях, служит хорошим упаковочным материалом).
В наше время, когда цены на энергоносители скачут вверх ежемесячно, стоит подумать именно про максимальную изоляцию помещений от разного рода потерь тепла.
Если посмотреть на подавляющее большинство зданий в городах СНГ в тепловизор зимой, то можно увидеть, как потоки тепла покидают квартиры через стены наружу. С теплоизоляцией из субъекта статьи картина резко меняется. На смену ярко-красным и жёлтым пятнам(горячий, высокий уровень потерь тепла) приходят оттенки синего (потерь тепла почти не наблюдается) и фиолетового.
Стоит ли объяснять, что на обогрев такого помещения понадобиться куда как меньше энергии и тепла? И всё это, благодаря покрытию толщиной в 12 сантиметров. Вот насколько низка теплопроводность этого материала!
Практически, абсолютная водонепроницаемость
Готовое изделие почти не впитывает воду, совсем не разбухает, слабо подвержено процессу капиллярной диффузии (объект статьи не гигроскопичен и будет хорошей изоляцией от осадков, выпадения росы, высокой влажности).
Так, например, известно, что объект совсем не гигроскопичен. Он не впитывает воду, даже будучи полностью погруженным в неё. Единственное явление проникновения воды в отдельные микроскопические гранулы материала. Но такое проникновение нельзя назвать значительным.
Даже при погружении в воду, объём поглощенной воды не будет превышать 3% от всего веса плиты. И даже в таком состоянии все прочие свойства материала не пострадают и останутся неизменными. Иначе говоря, изделие можно спокойно эксплуатировать в условиях с любой влажностью.
В то же время защита от проникновения водяного пара тоже радует. Скорость проникновения водяного пара в плиту составит не больше, чем 1% от самой скорости движения в воздушном пространстве вокруг пенополистирольной плиты. В то же самое время стоит отметить, что водяной пар и жидкая вода легко выходят из этого материала обратно.
Если соблюдать требования по эксплуатации, то можно использовать плиты для утепления цокольных этажей и подвальных стен.
Там вещество изолятора будет находиться в постоянном контакте с грунтом, но на его свойствах это не отразится.
Прочность
Специалисты отмечают высокую прочность готового изделия и на изгиб и на сжатие. В зависимости от технологии изготовления, упругая зона деформирования пенополистирола может включать в себя 10% от всего объёма плиты. Если использовать в качестве исходного сырья не полистирол, а другие полимеры, то упругость материала можно повысить или снизить. Прочность готового изделия на сжатие, может составлять до 25 т на метр квадратный. Фактически, эта прочность недостижима для многих других материалов, которые имеют сходное с пенополистиролом применение.
Химические свойства
Говоря о химических свойствах, стоит упомянуть тот факт, что пенопласт чрезвычайно устойчив к подавляющему большинству химических веществ. Именно благодаря этому этот изолятор универсален и может эксплуатироваться в разнообразных средах.
В нормативных документах указана подробная сводка по устойчивости к распространённым веществам:
- Раствор соли (или морская вода) — полностью устойчив;
- Мыла и растворённые в воде смачивающие вещества — наблюдается стабильная устойчивость;
- Отбеливатели — устойчив;
- Разведённые в воде кислоты — устойчив;
- Серная кислота — быстро растворяется;
- Распространённые щелочные металлы — устойчив;
- Органические растворители — не устойчив;
- Насыщенные алифатические углеводороды, медицинский бензин — не устойчив;
- Углеводородные энергоносители — не устойчив;
- Спирты — условно устойчив.
При использовании лакокрасочных материалов, необходимо учитывать возможную вероятность нарушения структуры пенополистирола.
Звукоизоляция
Акустические свойства материала сильно зависят от одного фактора способности материала к преобразованию энергии звуковой волны в тепло. И именно здесь как нельзя кстати оказываются высокие теплоизоляционные свойства субъекта статьи. Речь идёт о ячеистой структуре пенополистирола.
Для полной звукоизоляции помещения необходима пенополистирольная плита толщиной в два или три сантиметра. В дальнейшем, чем выше толщина плиты, тем выше соответствующие свойства.
Также стоит отметить, что свойства самого пенополистирола могут быть улучшены, если создавать объект с высоким содержанием открытых пор и гранул воздуха.
Биологические свойства
Говоря о биологической устойчивости субъекта статьи, стоит вспомнить о том, что он не представляет никакого интереса ни для микроорганизмов, ни для каких либо еще насекомых или животных. Он не создаёт для них благоприятную среду, не пригоден в еду ни одному живому существу, не подходит для грибков и плесени. Пенополистирол биологически нейтрален и устойчив.
Также следует отметить, что изделие совершенно не токсично ни для человека ни для прочих живых организмов. По крайней мере, на протяжении многих лет использования этого вещества в качестве упаковочного, никаких происшествий, отравлений или ранений не было отмечено. Из этого вещества делают упаковки для пищевых продуктов.
Огнестойкость
Пенополистирол устойчив к пожарам. Его температура горения в два раза превышает аналогичную у бумаги, и в 1.8 раза превышает температуру самовоспламенения необработанной древесины.
Пенополистирол горит, как и многие другие материалы, но сам по себе горение не поддерживает. Если открытого огня не будет, то пенополистирол потухнет через несколько секунд.
Также, отмечается высокая долговечность материала (не разлагается под действием окружающей среды, срок годности в нормальных условиях почти неограничен.
Виды производимого пенополистирола
Применение пенополистирола возможно разнообразными методами. Однако, свойства объекта говорят сами за себя.
Хорошее применение
- Теплоизоляция;
- Гидроизоляция и влагоизоляция.
- Звукоизоляция.
Критерии выбора
Наиболее интересным является употребление в строительстве. Однако, применение материала именно в этой области мало изучено. Существует ряд критики именно по этому вопросу. Однако, с развитием технологии каркасного строительства, изделие активно используется на малых и крупных строительных предприятиях.
Пенополистирол в строительствеУже исходя из вышеописанного технического процесса, можно сделать вывод о том, что этот компонент будет чрезвычайно лёгким и недорогим, и может широко применяться в строительном производстве в качестве универсального утеплителя для стен или упаковочного материала.
Как и любой другой строительный материал, пенополистирол подвергался многочисленным проверкам и исследованиям. Благодаря этим исследованиям, свойства пенополистирола уже полностью изучены. Пенополистирол — объект, которым пользуются в строительстве на протяжении длительного периода времени.
Выбор конкретной марки пенополистирола должен зависеть от условий эксплуатации изделия.
Видео
Посмотрите видео о технологии производства, свойствах и способах применения полистирола
% PDF-1.4
%
659 0 объект
>
endobj
xref
659 286
0000000016 00000 н.
0000009975 00000 н.
0000010077 00000 п.
0000013499 00000 п.
0000013536 00000 п.
0000013708 00000 п.
0000013898 00000 п.
0000014012 00000 п.
0000025531 00000 п.
0000025721 00000 п.
0000025913 00000 п.
0000026101 00000 п. 0000026287 00000 п.
0000026473 00000 п.
0000026664 00000 н.
0000026853 00000 п.
0000027043 00000 п.
0000027232 00000 н.
0000027423 00000 п.
0000027614 00000 п.
0000027806 00000 п.
0000027998 00000 н.
0000028188 00000 п.
0000028377 00000 п.
0000028564 00000 п.
0000028751 00000 п.
0000028940 00000 п.
0000029130 00000 п.
0000029319 00000 п.
0000029507 00000 п.
0000029699 00000 н.
0000029891 00000 п.
0000030083 00000 п.
0000030275 00000 п.
0000030466 00000 п.
0000030656 00000 п.
0000030847 00000 п.
0000031037 00000 п.
0000031229 00000 п.
0000031421 00000 п.
0000042037 00000 п.
0000042224 00000 п.
0000042412 00000 п.
0000042600 00000 п.
0000042790 00000 н.
0000042978 00000 п.
0000043168 00000 п.
0000043356 00000 п.
0000043544 00000 п.
0000043730 00000 п.
0000043919 00000 п.
0000044106 00000 п.
0000044293 00000 п.
0000044482 00000 п.
0000044670 00000 п.
0000044856 00000 п.
0000045044 00000 п.
0000045233 00000 п.
0000045422 00000 п.
0000045609 00000 п.
0000045798 00000 п.
0000045987 00000 п.
0000046177 00000 п.
0000046369 00000 п.
0000046559 00000 п.
0000046747 00000 п.
0000046935 00000 п.
0000047125 00000 п.
0000047315 00000 п.
0000047504 00000 п.
0000047694 00000 п.
0000047883 00000 п.
0000048072 00000 п.
0000048261 00000 п.
0000048450 00000 п.
0000048641 00000 п.
0000048831 00000 н.
0000049022 00000 н.
0000049214 00000 п.
0000049405 00000 п.
0000049596 00000 п.
0000060526 00000 п.
0000060712 00000 п.
0000060900 00000 п.
0000061089 00000 п.
0000061276 00000 п.
0000061465 00000 п.
0000061654 00000 п.
0000061840 00000 п.
0000062030 00000 п.
0000062221 00000 п.
0000062412 00000 п.
0000062533 00000 п.
0000062630 00000 н.
0000062822 00000 п.
0000063017 00000 п.
0000063208 00000 п.
0000063392 00000 п.
0000063583 00000 п.
0000063774 00000 п.
0000063961 00000 п.
0000064152 00000 п.
0000064343 00000 п.
0000064534 00000 п.
0000064725 00000 п.
0000064916 00000 п.
0000065107 00000 п.
0000065297 00000 п.
0000065488 00000 н.
0000065679 00000 п.
0000065870 00000 п.
0000076658 00000 п.
0000076850 00000 п.
0000077036 00000 п.
0000077225 00000 п.
0000077411 00000 п.
0000077599 00000 п.
0000077789 00000 п.
0000077976 00000 п.
0000078164 00000 п.
0000078355 00000 п.
0000078543 00000 п.
0000078731 00000 п.
0000078918 00000 п.
0000079105 00000 п.
0000079297 00000 п.
0000079485 00000 п.
0000079676 00000 п.
0000079861 00000 п.
0000080050 00000 п.
0000080240 00000 п.
0000080428 00000 п.
0000080617 00000 п.
0000080808 00000 п.
0000080997 00000 п.
0000081186 00000 п.
0000081379 00000 п.
0000081564 00000 н.
0000081749 00000 п.
0000081935 00000 п.
0000082122 00000 п.
0000082308 00000 п.
0000082497 00000 п.
0000082686 00000 п.
0000082875 00000 п.
0000083066 00000 п.
0000083255 00000 п.
0000083444 00000 п.
0000083633 00000 п.
0000093333 00000 п.
0000093521 00000 п.
0000093705 00000 п.
0000093893 00000 п.
0000094079 00000 п.
0000094268 00000 п.
0000094457 00000 п.
0000094554 00000 п.
0000094745 00000 п.
0000094933 00000 п.
0000095120 00000 п.
0000095307 00000 п.
0000095496 00000 п.
0000095687 00000 п.
0000095784 00000 п.
0000095973 00000 п.
0000096156 00000 п.
0000096345 00000 п.
0000096533 00000 п.
0000096721 00000 п.
0000096907 00000 п.
0000097087 00000 п.
0000097275 00000 п.
0000097462 00000 п.
0000097646 00000 п.
0000097837 00000 п.
0000097934 00000 п.
0000098121 00000 п.
0000098313 00000 п.
0000098505 00000 п.
0000098695 00000 п.
0000098889 00000 п.
0000099077 00000 п.
0000099265 00000 п.
0000099453 00000 п.
0000099644 00000 п.
0000099833 00000 н.
0000100024 00000 н.
0000100215 00000 н.
0000100404 00000 н.
0000100593 00000 н.
0000100776 00000 н.
0000100965 00000 н.
0000101151 00000 н.
0000101340 00000 н.
0000101532 00000 н.
0000101721 00000 н.
0000101913 00000 н.
0000102103 00000 п.
0000102293 00000 п.
0000102485 00000 н.
0000102672 00000 п.
0000102864 00000 н.
0000113790 00000 н.
0000114047 00000 н.
0000114587 00000 н.
0000114844 00000 н.
0000115330 00000 н.
0000115414 00000 н.
0000115671 00000 н.
0000116313 00000 н.
0000116400 00000 н.
0000116870 00000 н.
0000117304 00000 н.
0000117929 00000 н.
0000117966 00000 н.
0000118078 00000 н.
0000118175 00000 н.
0000118365 00000 н.
0000118556 00000 н.
0000118744 00000 н.
0000118933 00000 н.
0000119123 00000 н.
0000119306 00000 н.
0000119497 00000 н.
0000119686 00000 н.
0000119875 00000 н.
0000120066 00000 н.
0000120257 00000 н.
0000120447 00000 н.
0000120637 00000 п.
0000120826 00000 н.
0000121015 00000 н.
0000121206 00000 н.
0000121396 00000 н.
0000121588 00000 н.
0000121776 00000 н.
0000132649 00000 н.
0000142519 00000 н.
0000142747 00000 н.
0000146184 00000 н.
0000146299 00000 н.
0000148948 00000 н.
0000154432 00000 н.
0000154772 00000 н.
0000155002 00000 н.
0000155376 00000 н.
0000155662 00000 н.
0000160030 00000 н.
0000160151 00000 п.
0000160437 00000 н.
0000160534 00000 п.
0000160954 00000 н.
0000161342 00000 н.
0000161716 00000 н.
0000162088 00000 н.
0000162163 00000 н.
0000162470 00000 н.
0000162545 00000 н.
0000162850 00000 н.
0000162925 00000 н.
0000163022 00000 н.
0000163220 00000 н.
0000163295 00000 н.
0000163392 00000 н.
0000163582 00000 н.
0000163983 00000 н.
0000164375 00000 н.
0000164496 00000 н.
0000164687 00000 н.
0000164877 00000 н.
0000165062 00000 н.
00001
Что такое пенополистирол? — STYRO
По сути, это то, что вы часто видите и используете в повседневной жизни — например, чашки из пенополистирола, упаковка, изоляция и многое другое. Фактически он состоит из 98% воздуха и 2% полистирола. Его пропаривают таким образом, что он становится пеной в особой форме. Что хорошего в EPS, так это то, что его можно полностью повторно использовать и перерабатывать, а значит, он экологичен.
STYRO Пенополистирол «EPS» — это жесткий пенополистирол, полученный из нефти. под воздействием пара он увеличится в 40 раз по сравнению с исходным размером, что делает его чрезвычайно универсальным продуктом.
Каковы общие характеристики EPS?
- Огнестойкий
- 100% перерабатываемый
- Легкий
- Стабильный
- Прочный
- Плавучий
- Прост в обращении
- Прочный и гибкий
- Амортизатор
- Гаситель вибрации
- Устойчив к влаге
- Стоимость- эффективный
- Высокая теплоизоляция
Каковы преимущества использования пенополистирола?
EPS — прекрасная альтернатива, если вы хотите использовать дерево, войлок, резину или стекловолокно. Вы можете заменить сырье пенополистиролом и не беспокоиться о том, что качество упадет, потому что оно станет еще лучше.
EPS можно придать любой форме, которая вам нравится. Используя другое оборудование, вы сможете вырезать и придавать форму пенопласту и материализовать свои визуальные эффекты.
Это идеальный продукт для упаковки, поскольку он может противостоять ударам, а также воде или другим внешним элементам.
Это, несомненно, рентабельно — производители пенополистирола, такие как STYRO, могут эффективно доставлять и производить вашу продукцию из пенополистирола, тем самым экономя ваше время и деньги.
Чтобы узнать, как EPS может быть полезен для ваших проектов и бизнеса, свяжитесь с нами в STYRO, и мы доставим вам все это. Благодаря нашим накопленным знаниям и многолетнему опыту мы уже заняли позицию на рынке, которая многое говорит о нашем отличном преимуществе по сравнению с другими производителями пенополистирола. Мы уже работали с известными брендами по всему ОАЭ и стремимся и дальше оставаться лидером в производстве пенополистирола.
ДАТА | HS_CODE | Описание продукта | Торговая марка | Страна | Вес нетто | Статистическая стоимость | Место | Имя грузоотправителя | Имя получателя | |
---|---|---|---|---|---|---|---|---|---|---|
2017 -09-04 | 3921110000 | Плиты из пенополистирола (пенопласт), теплоизоляция, прямоугольной формы МАРК ППС10, плотность 8.4 кг / м3, изготовлен по ГОСТ 15588-2014, для производства упаковки холодильного оборудования STYROFOAM PPS10 IVF 1000H500h25 ООО «Новопласт-ЮГ»: О | *** | РОССИЯ | 705,3 | 2611,97 | *** | ***** | ***** | |
2017-09-05 | 8480710000 | Формы для резины и пластмасс для литья-выдувания или под давлением, B / U MOLD / б / у для производства ДНК УПАКОВКА 41039291 Холодильники бытовые, пенополистирол (пенополистирол).Размеры формы 1480х2280х390 мм.![]() | *** | РОССИЯ | 5580 | 5393,87 | *** | ***** | ***** | |
2017-09-05 | 8708999709 | Опытные образцы для автомобиля LADA XRAY, ТИП: 749488682R 2 шт., Защитная прокладка НАПОЛЬНАЯ КОНСТРУКЦИЯ ЗАДНЯЯ ЧАСТЬ из формованного пенополистирола, повторяет контур ПОЛ ЗАДНЯЯ КАБИНА В A / M, C технологические отверстия, FELTANY | LADA | LADA0.44 | 5,25 | Ашаффенбург | ***** | ***** | ||
2017-09-13 | 3214101009 | Мастичные защитно-декоративные покрытия для изделий из пенополистирола и пенополиуретана ведра 25 КГ.ПРЕДСТАВЛЯЕТ материал на водной основе негорючий НЕ ПРИМЕНЯЕТСЯ К ОПАСНЫМ МАТЕРИАМ.ПРЕДНАЗНАЧЕН наносится на декоративную поверхность ТЭ | *** | РОССИЯ | 2025 | 2975,37 | *** | ***** | ***** | |
2017-09-13 | 3921110000 | Плиты из пенополистирола (пенопласт), теплоизоляция, прямоугольной формы МАРК ППС10, плотность 8.![]() | *** | РОССИЯ | 748.75 | 2830,94 | *** | ***** | ***** | |
2017-09-13 | 39230 | ЛИСТ ДЛЯ УПАКОВКИ ПИЩЕВЫХ ПРОДУКТОВ ИЗ ПЛАСТИКА — пенополистирола ПОДЛОЖКА АВ-20 «А» (225х260х44 ) (NC * 200) КОНТЕЙНЕР PP 500мл (UPh2000 шт.) Подложка G-4 «A» AVT (250х275х45) (NC * 150) Подложка P D-31 «AB» C (225х235h40) (NC * 250) Подложка F F- 3 | *** | РОССИЯ | 2864.18 | 9135,11 | *** | ***** | ***** | |
2017-09-13 | 3916 | 0 | ПРОФИЛЬ пенополистирол предназначен для стен и потолков DSMSL00300, профили из пенополистирола (ООО «НМС», РОССИЯ) LX-30 Код товара: DSMSL00400, профили из пенополистирола (ООО «НМС», РОССИЯ) LX-40 Код товара: DSMSL00350, профили из пенополистирола (ООО | *** | РОССИЯ | 367,2 | 1206,7 | *** | ***** | ***** |
2017-09-13 | 3921110000 | Плиты из пенополистирола (пенопласт), теплоизоляция прямоугольной формы МАРК ППС10, плотность 8.![]() | *** | РОССИЯ | 748.75 | 2830,94 | *** | ***** | ***** | |
2017-09-13 | 39230 | ЛИСТ ДЛЯ УПАКОВКИ ПИЩЕВЫХ ПРОДУКТОВ ИЗ ПЛАСТИКА — пенополистирола ПОДЛОЖКА АВ-20 «А» (225х260х44 ) (NC * 200) КОНТЕЙНЕР PP 500мл (UPh2000 шт.) Подложка G-4 «A» AVT (250х275х45) (NC * 150) Подложка P D-31 «AB» C (225х235h40) (NC * 250) Подложка F F- 3 | *** | РОССИЯ | 2864.18 | 9135,11 | *** | ***** | ***** | |
2017-09-13 | 3916 | 0 | ПРОФИЛЬ пенополистирол предназначен для стен и потолков DSMSL00300, профили из пенополистирола (ООО «НМС», РОССИЯ) LX-30 Код товара: DSMSL00400, профили из пенополистирола (ООО «НМС», РОССИЯ) LX-40 Код товара: DSMSL00350, профили из пенополистирола (ООО | *** | РОССИЯ | 367,2 | 1206,7 | *** | ***** | ***** |
Переработка пенополистирола с использованием природных растворителей
1.Введение
Переработка природных ресурсов и отходов является наиболее важным процессом в концепции зеленой химии. В последнее время использование биомассы стало важной темой, в то время как переработка нефтяных ресурсов должна получить аналогичное внимание. Пенополистирол (EPS) широко используется в упаковочных и строительных материалах, а также для электроизоляции и теплоизоляции из-за небольшого веса и низкой теплопроводности и электропроводности. Пористость EPS очень высока, так как 98% кажущегося объема пористы.В настоящее время в мире производится более 2 миллионов тонн пенополистирола в год [1], а скорость вторичного использования материалов среди товарных пластиков относительно высока [2].
Для рециркуляции EPS требуется плавление [2,3] или обработка растворителем [4,5] для уменьшения объема и последующего изменения формы, как показано на Рисунке 1. Процесс плавления прост, но дает некоторые химическое разложение и не может избежать снижения качества исходного полистирола (ПС), поэтому обработка растворителем во многих отношениях более желательна для эффективной системы рециркуляции.Хотя существуют различные растворители для PS, например углеводороды, алкилгалогениды, ароматические соединения, сложные эфиры и кетоны, растворители на нефтяной основе не являются благоприятными для окружающей среды. Лимонен, входящий в состав цитрусовых масел, был получен на основе вышеупомянутой концепции и является пионером природных растворителей для EPS [6-8]. В последнее время переработка EPS с использованием лимонена была реализована на практике в полупромышленном масштабе, однако для извлечения 100 мл лимонена необходима кожура, соответствующая приблизительно 1000 апельсинам [9].За исключением лимонена, существует несколько сообщений о природных растворителях для EPS. В этой главе основное внимание уделяется растворению PS в монотерпенах, содержащихся в естественных условиях, включая лимонен, в частности, взаимосвязи между химической структурой и растворяющей способностью PS. Кроме того, описаны свойства ПС, переработанного с использованием этих растворителей, в сравнении со свойствами исходного ПС.
Рисунок 1.
Система переработки материалов EPS.
2. Природные монотерпены и их растворяющая способность для PS
Hattori et al.[10] обратили внимание на тот факт, что, поскольку лимонен является одним из терпенов, ожидается, что другие монотерпены и терпеноиды также будут растворять PS. Терпен — это биомолекулярный углеводород, структурная основа которого содержит изопреновую единицу. В соответствии с номером изопреновой единицы они называются монотерпеном (C10), сесквитерпеном (C15), дитерпеном (C20), сестертерпеном (C25) и т. Д. Многие монотерпены являются жидкими при комнатной температуре и являются основными компонентами эфирных масел. В частности, листовые масла видов Abies sachalinensis и Eucalyptus , у которых рост происходит сравнительно быстро, могут быть подходящей биомассой, поскольку в настоящее время они не используются эффективно и содержат много монотерпенов.В таблице 1 приведены некоторые жидкие монотерпены и терпеноиды, выбранные с точки зрения степени содержания в их масле листьев [11-13]. Оба существенно отличаются. d — Лимонен много содержится в Abies sachalinensis , но немного в Eucalyptus . Наибольшее количество борнилацетата в Abies sachalinensis не содержится в Eucalyptus . Напротив, 1,8-цинеол в большом количестве встречается в Eucalyptus , тогда как не встречается совсем в Abies sachalinensis .
Терпен и терпеноид | Доля содержания (%) а | ||
Abies sachalinensis | Эвкалипт | Ацетилсодержащий Born | |
d -Лимонен | 22,6 | 3,1 | |
β -фелландрен | 15,6 | 0 | |
α -пинен | 13.3 | 37,9 | |
β -Пинен | 9,7 | 0,5 | |
Мирцен | 1,9 | 0,4 | |
p -Цимен | 0,4 | , 8-Цинеол0 | 29,9 |
Таблица 1.
Компоненты в масле листьев Abies sachalinensis и Eucalyptus.
a) Процент масла листьев в 100 мл, измеренный с помощью ГХ-МС [11-13].
Во-первых, некоторые структурные изомеры и аналоги d -лимонена, как показано на рисунке 2, были изучены на растворяющую способность для PS [10]. Методика эксперимента заключается в следующем. Известный вес небольшого кусочка коммерческой пленки ПС со среднечисленной молекулярной массой (M¯n) 1,2 × 10 5 помещали в 0,5 мл каждого терпена при 50 ° C, и наблюдали за поведением ПС. методом поляризационной микроскопии под скрещенными николями. О растворении судили по исчезновению двойного лучепреломления детали из PS.Дополнительный кусок при необходимости ставили после достижения полного растворения. В таблице 2 растворяющая способность терпенов указана как масса растворенного PS на 100 г каждого терпена. Все эти терпены способны растворять более 120 г ПС на 100 г их. Эти значения выше, чем у толуола, который является одним из нефтяных растворителей для PS. Эти шесть терпенов, за исключением цимола p , являются структурными изомерами с разными положениями связи C = C, поэтому они будут иметь одинаковую растворяющую способность друг друга.Этот результат привел к взаимосвязи между структурой и растворяющей способностью, согласно которой положение связи C = C не сильно влияет на растворяющую способность. Растворимость PS в цимене p значительно выше, чем в других терпенах, потому что цимен p является, как описано ниже, ароматическим углеводородом, который имеет аналогичную химическую структуру с PS.
Рис. 2.
Структура d-лимонена и некоторых его изомеров и аналогов.
Растворитель | Растворимость (г / 100 г растворитель) a |
α -Терпинен | 130 |
γ -Terpin | |
d -Лимонен | 127 |
Терпинолен | 125 |
α -Фелландрен | 125 |
β -Phellandrene 122 | 9036 p. -Cymene212 |
Толуол b | 117 |
Таблица 2.
Растворимость PS в нескольких монотерпенах при 50 ° C.
а) По ссылке [10].
б) Для сравнения был использован один из растворителей на нефтяной основе.
Как показано в таблице 1, в масле листьев Eucalyptus содержится значительное количество 1,8-цинеола. Поэтому следующее исследование растворяющей способности природных растворителей для PS было направлено на 1,8-цинеол и некоторые родственные кислородсодержащие терпеноиды [10,14]. На рис. 3 и в таблице 3 представлены химическая структура терпеноидов и их растворяющая способность для PS, соответственно.
Рис. 3.
Структура 1,8-цинеола и некоторых кислородсодержащих терпеноидов.
Растворитель | Растворимость (г / 100 г растворителя) a |
1,8-цинеол | 55 |
Терпинен-4-ол | 39 |
α -Терпинеол | 41 |
2- p -Цименол | 105 |
Геранилацетат | 174 |
Таблица 3.
Растворимость PS в некоторых кислородсодержащих терпеноидах при 50 ° C.
a) Цитируется по ссылкам [10] и [14].
Обычно неполярные молекулы, такие как PS, не взаимодействуют с полярным растворителем. Терпинен-4-ол и α -терпинеол имеют такую высокую полярную составляющую, как гидроксильная группа, поэтому растворимость PS в них (около 40 г / 100 г растворителя) ниже, чем в соответствующем терпинене и терпинолен без гидроксильной группы (около 130 г / 100 г растворителя, таблица 2).Кислород 1,8-цинеола относится не к гидроксильной, а к эфирной группе. Предполагается, что более высокая растворимость PS в 1,8-цинеоле (55 г / 100 г растворителя), чем в терпинен-4-оле и α -терпинеоле, приписывается более низкой полярности эфирной группы по сравнению с гидроксильная группа. Высокая растворяющая способность 2-p -цименола (105 г / 100 г растворителя), несмотря на наличие гидроксильной группы, может быть связана с присутствием ароматического кольца, как упомянуто выше.
Рисунок 4.
EPS, усадка α-терпиненом (а) и геранилацетатом (б) [10].
Геранилацетат показывает наивысшую растворяющую способность 174 г на 100 г. На рис. 4 показан вид растворения ЭПС α -терпиненом (а) и геранилацетатом (б) [10]. Геранилацетат, по-видимому, более эффективен, чем α -терпинен в отношении способности сокращать EPS. Похоже, что высокая растворяющая способность геранилацетата основана на его гибкой линейной структуре, которая более доступна для внутренней части объемного ПС по сравнению с циклическими терпенами в таблице 2.Поэтому для подтверждения этого была изучена растворяющая способность нескольких ациклических монотерпенов. Геранилацетат, цитронеллилацетат и мирцен содержатся в эфирных маслах рода Picea и других [11], а цитраль и цитронеллаль входят в состав масел цитрусовых [15]. Как показано в таблице 4, геранилацетон, геранилформиат и цитронеллилацетат обладают такой же растворяющей способностью, как и геранилацетат.
Рис. 5.
Структура нескольких ациклических терпенов и терпеноидов.
Растворитель | Растворимость (г / 100 г растворителя) a |
Геранилацетон | 160 |
Геранилформиат | 1757 |
156 | |
Цитраль | 109 |
Цитронеллаль | 125 |
Мирцен | 101 |
Таблица 4.
Растворимость PS в нескольких ациклических терпеноидах при 50 ° C.
a) Частично цитируется из ссылки [10].
Эти значения выше, чем у типичных циклических монотерпенов в таблице 2. Относительно низкая растворяющая способность цитраля и цитронеллаля по сравнению с ациклическими сложными эфирами может быть связана с наличием концевой альдегидной группы полярного фрагмента, который вызывает восстановление доступность гидрофобной матрицы ПС. Неожиданно мирцен не показывает очень высокую растворяющую способность 101 г на 100 г, хотя он является неполярным углеводородом.Структура концевого сопряженного диена, вероятно, не настолько гибка, чтобы проникать в матрицу ПС. Эти результаты ясно показывают, что гибкие линейные терпены обладают более высокой растворяющей способностью для PS, чем циклические терпены.
Ряд этих систематических экспериментальных результатов вызывает один фундаментальный вопрос: какой растворяющей способностью обладают сами эфирные масла? Масло Abies можно легко приготовить путем кипячения с обратным холодильником в течение 6 часов в воде и последующей перегонки с водяным паром листьев Abies sachalinensis [14]. Масло эвкалипта коммерчески доступно от Tokyo Chemical Industry, Inc., Япония. Растворимость PS в маслах Abies и Eucalyptus составляла 85 г и 96 г на 100 г из них [14], соответственно, как показано в таблице 5. Согласно отчетам Yatagai et al. [11,12], Масло листьев Abies содержит 27% борнилацетата и 23% пиненов, структура и растворяющая способность которых следующие.
Рис. 6.
Структура борнилацетата и пиненов.
Растворитель | Растворимость (г / 100 г растворителя) a |
Abies листовое масло | 85 |
эвкалиптовое масло | |
Борнилацетат | 67 |
α -Пинен | 44 |
β -Пинен | 48 |
Таблица 5.
Растворимость PS в эфирных маслах и некоторых бициклических терпенах при 50 ° C.
a) Частично цитируется из ссылки [10].
Растворимость PS в борнилацетате и обоих пиненах составляет менее половины от растворимости PS в изомерах лимонена. Борнилацетат и пинены имеют объемную бициклическую структуру, которая, вероятно, будет невыгодной для проникновения в ПС. В результате масло листьев Abies , содержащее примерно 50% этих трех терпенов в сумме, не имеет такой высокой растворяющей способности для PS.Поскольку масло Eucalyptus также содержит такие бициклические терпены, как 30% 1,8-цинеола и 38% α -пинена, оно не является очень сильным растворителем для самого PS. Однако оба масла по-прежнему обладают растворяющей способностью почти 100 г для PS на 100 г из них, так что они будут подходящим растворителем для вторичного использования PS.
3. Связь между параметром растворимости и растворяющей способностью монотерпенов
В качестве общего стандарта для суждения о том, что данное растворенное вещество растворимо или нерастворимо в растворителе, существует метод сравнения «параметра растворимости» растворенного вещества с растворитель.Хильдебранд первым разработал теорию этой концепции [16], а затем Хансен [17], Бартон [18], Хофтизер и Кревелен [19,20] и др. развили эту теорию. Параметр растворимости ( δ ) вещества определяется как:
, где E coh и V — энергия когезии (= энергия испарения) и молярный объем вещества, соответственно. V рассчитывается на основе молекулярной массы и плотности вещества. E coh может быть получен экспериментально для летучего вещества, но обычно получается из теоретического подхода.Хансен [17] считал, что E coh состоит из трех типов энергии, полученных из следующих сил взаимодействия:
, где E d , E p и E h — энергия дисперсионных сил, полярных сил и водородной связи соответственно. Затем уравнение (1) модифицируется с использованием соответствующих компонентов параметра растворимости, δ d , δ p и δ h , для каждой силы следующим образом:
С учетом этих межмолекулярных взаимодействий, Хофтизер и Кревелен [19] выразили их компоненты следующим образом:
δd = ∑FdiV, δp = ∑Fp2iV и δh = EhiVE4, где Fdi, Fpi и Ehia — параметры дисперсионных сил, полярных сил и водородных связей. , соответственно, отражающие вклад структурных групп вещества.Среди параметров группового вклада, установленных Hoftyzer и Krevelen [20], параметры, относящиеся к терпенам, показаны в таблице 6.
Структурная группа | Fdi (J1 / 2 · м3 / 2 · моль − 1) a | Fpi (J1 / 2 · м3 / 2 · моль − 1) a | Ehi (Дж · моль − 1) a |
−CH 3 | 0,42 | 0 | 0 |
−CH 2 — | 0.27 | 0 | 0 |
0,08 | 0 | 0 | |
-0,07 | 0 | 0 | |
= CH 2 | 0,40 | 0 | |
= CH− | 0,20 | 0 | 0 |
0,07 | 0 | 0 |
Таблица 6.
Параметры группового вклада, связанные с терпенами.
a) По ссылке [20].
b) Если две идентичные полярные группы присутствуют в симметричном положении, значение δ p должно быть умножено.
Структурная группа | Fdi (J1 / 2 · м3 / 2 · моль − 1) | Fpi (J1 / 2 · м3 / 2 · моль − 1) | Ehi (Дж · моль − 1) | |
−CH 3 × 4 | 1.68 | 0 | 0 | |
−CH 2 — × 3 | 0,81 | 0 | 0 | |
= CH− × 2 | 0,40 | 0 | 0 | |
0,14 | 0 | 0 | ||
−COO− | 0,39 | 0,49 | 7000 | |
Сумма | 3,42 | 0,49 | 7000 | 7000 |
В соответствии с таблицей 6 параметры группового вклада геранилацетата вычислены, как показано в таблице 7. Поскольку молекулярная масса ( MW ) и плотность ( d ) геранилацетата составляют 196,29 г / моль и 0,909 г / моль. см 3 , соответственно молярный объем V оценивается как 2,159 × 10 −4 м 3 / моль. Следовательно, компоненты параметра растворимости:
δd = ∑FdiV = 3.42J1 / 2⋅m3 / 2⋅mol − 12,159 × 10−4m3⋅mol-1 = 15,8 МПа1 / 2, δp = ∑Fpi2V = 0.490J1 / 2⋅м3 / 2⋅моль − 12,159 × 10−4м3⋅моль-1 = 2,27 МПа1 / 2, и Manufacturing Home ЛИТЬЕ МЕТАЛЛА ПРОЦЕССЫ Принципы литья металлов Литье металла Операция по литью металла Влияние газов на металлическую отливку Дизайн литья металла Расходные формы для литья под давлением Литье в песчаные формы Литье гипсовых форм Керамическое литье Литье в пресс-форму Вакуумное литье или V-образный процесс Литье по выплавляемым моделям Постоянное литье формы Базовое постоянное литье в пресс-форму Слякоть литья Литье под давлением Литье в постоянную вакуумную форму Литье под давлением Горячее литье под давлением Холодное литье под давлением Истинное центробежное литье Полукентробежное литье Центрифужное литье Литье слитков Непрерывное литье ПРОИЗВОДСТВО ПРОЦЕССЫ Обработки металлов давлением Металлопрокат Металлическая ковка Металл Экструзия Рисунок Металла Листовой металл Порошковые процессы | В процессе литья пенополистирола песчаная форма упакован вокруг узора из полистирола, представляющего металлическую отливку, изготовлено.Узор не снимается, а расплавленный металл заливается в узор, который испаряется от тепла металла. Жидкий металл забирает место испаренного полистирола и отливка затвердевает в песчаной форме. В индустрии литья металлов этот процесс известен как процесс по выпадению пены, литье по схеме испарения или процесс полной формы. Большой с его помощью можно изготавливать различные отливки из различных материалов и размеров. техника. Детали, произведенные в обрабатывающей промышленности с использованием этого процесса, включают: коленчатые валы, головки цилиндров, основания машин, коллекторы и блоки двигателей. ПроцессПервым этапом процесса литья под давлением является производство полистирола. шаблон. Для небольших производственных партий выкройку можно вырезать из больших частей материал пенополистирол и собран вместе. Для крупного промышленного производства процессов, выкройка будет лепиться. Матрица, часто сделанная из алюминия, используется для этот процесс. Шарики полистирола помещаются в фильеру и нагреваются, они расширяются от тепло и вспененный материал принимает форму матрицы.В зависимости от сложности отливки некоторые из этих полистирольных секции, возможно, придется склеить вместе, чтобы сформировать узор. В большинстве случаев узор покрыт огнеупорным составом, это поможет создать хорошую поверхность отделка на металлическом литье. Помимо самой отливки, рисунок из пенопласта также будет Включите наливную чашку и литниковую систему.
Затем выкройку помещают в колбу, и вокруг нее набивают формовочный песок.В песок может содержать или не содержать связующие вещества, в зависимости от конкретного процедура изготовления.
Затем расплавленный металл заливают в форму без удаления шаблона. В жидкий металл испаряет рисунок из полистирола, когда он течет через полость формы. Любой продукт, оставшийся от испаренного полистирола, впитывается в формовочный песок.
Затем расплавленному металлу дают затвердеть в песчаной форме.После затвердевания отливка снимается.
Свойства и особенности производства Отливкой из пенополистирола
|